生産の拡大と工場の変遷
岡山県南の干拓地・興除村で誕生した岡山工場。
農機機械の発展と共に規模を拡大し、江並の現工場へ移転。
独自の管理システムで高品質で効率の良いものづくりを展開しています。
レイアウトの再編成や生産ラインの移管を繰り返しながら、
現在までに様々な種類の農業機械を混流生産してきました。
- 1961年
- 耕うん機の生産主力工場として、
江並の現工場へ移転 - 1969年
- バインダー生産のための組立工場を増築
- 1975年
- コンバイン生産のための組立工場を増築
- 1980年
- 創業60周年となり、現事務所を新築
- 1987年
- 整備センターを開所
- 1989年
- 子会社セイレイトータルサービス(株)を立上げ
- 1991年
- 開発の拠点となるテクニカルセンターを開設
- 2003年
- 田植機生産のための全面的な
工場レイアウト再編成 - 2013年
- トラクター生産のための
全面的な工場レイアウト再編成
工場MAP岡山工場って
こんなところ

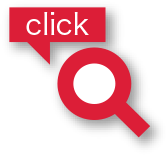
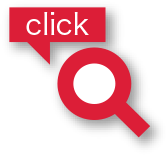
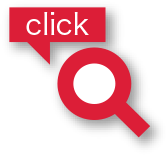
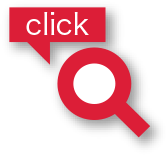
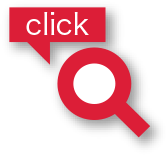
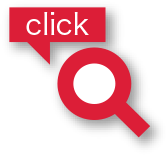
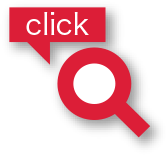
目指せ!
「AI」「ロボット」を駆使した
万能な工場
溶接や塗装・組立・検査など、全ての作業がロボットに置き換えられた未来の工場。高品質な製品を、計画通りに出荷できる仕組みを整えています。
お客様のご要望からAIが最適な製品を自働で導き出し、工場へのオーダーや部品の調達などを最適化して、最短納期でお客様に製品をお届けすることを目指します。
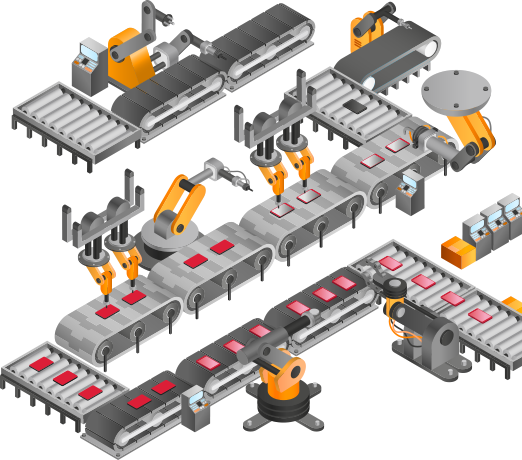