アグリ事業本部 開発統括部
ヤンマーテクニカルレビュー
ヤンマーコンバインの操舵システムについて(フルタイムドライブシステム「FDS」)
はじめに
平成18年、ヤンマーの「コンバイン等の強制デフ式操舵システム」が「大阪優秀発明大賞」を受賞した。この賞は、平成15~17年の3年間連続で松下電器産業(株)が受賞していた賞であるが、並み居る大阪の企業を制し、科学技術発展のための優秀な発明として認められた。また、旋回という動作に駆動力を与えた新操舵システムが農業機械の分野から抜け出して認知された記念すべき日となった。(資料1)
ヤンマーは昭和46年からコンバインという穀物収穫機を商品化してきたが、当初直進系ではクラッチを踏んで変速する機構が、また、旋回系はサイドクラッチを切ってブレーキをかけて旋回する機構が主流であった。この操舵方式を「クラッチ&ブレーキ方式」と呼び採用していた。(資料2)
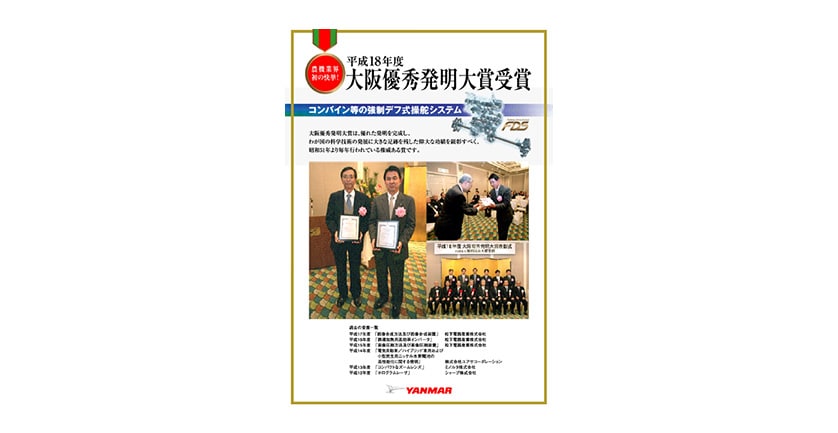
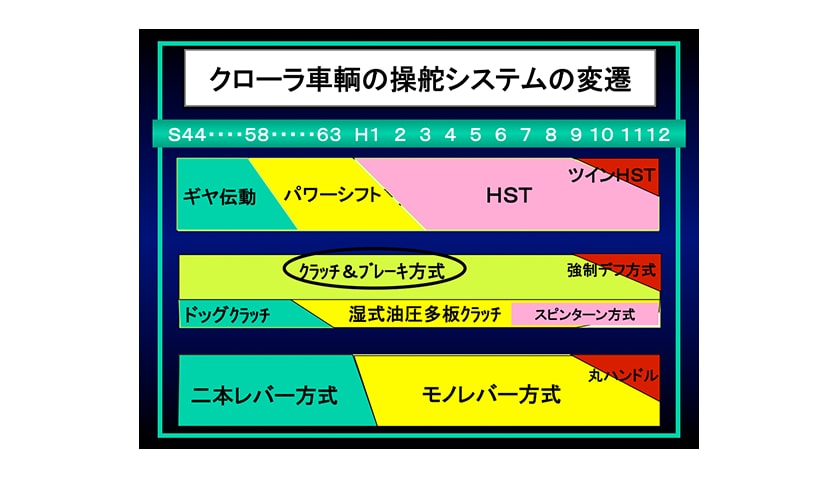
しかし、籾を稲から分離する脱穀部と呼ばれる作業部位の技術開発が進み、作業能率が向上するにつれて、車両の作業速度が高速化していった。これにより、直進系の変速方式は無段化へと切り替えられ、パワーシフト(多段摩擦板伝動)やHSTといった油圧式無段変速へと変遷していった。これに対し、旋回系では大きな変革がなかった。
弊社は、作業速度の高速化に対する旋回系の改善として、同じ履帯方式を採用している戦車をモデルにして検討を重ねた結果、この「強制デファレンシャル方式」トランスミッションにたどり着いた。(資料3)ただし、戦車のステアリング操作方式を採用した場合、
- 前進状態でハンドルを右に切ると右に旋回
- 後進状態でハンドルを右に切ると左に旋回
となる。戦車の場合は高速で直進走行することが主目的であり、バックでの車庫入れなどの頻度は少ないため、乗用車とは逆のハンドル操作になっている。(資料4)コンバインの場合はその作業体系から前後進での旋回操作頻度が多いため、乗用車感覚の操作性が必要となる。そこで弊社が開発したのが、「円錐式ステアリングリンク」である。さらに、それまで二本または一本のレバーで実施していたステアリング操作方式を見直してハンドル化することで、より乗用車感覚の操作に仕上げることができた。

≪参考文献≫メカニックブックス14レオパルト戦車 発行所:原書房、著者:浜田 一穂
1987年9月10日発行
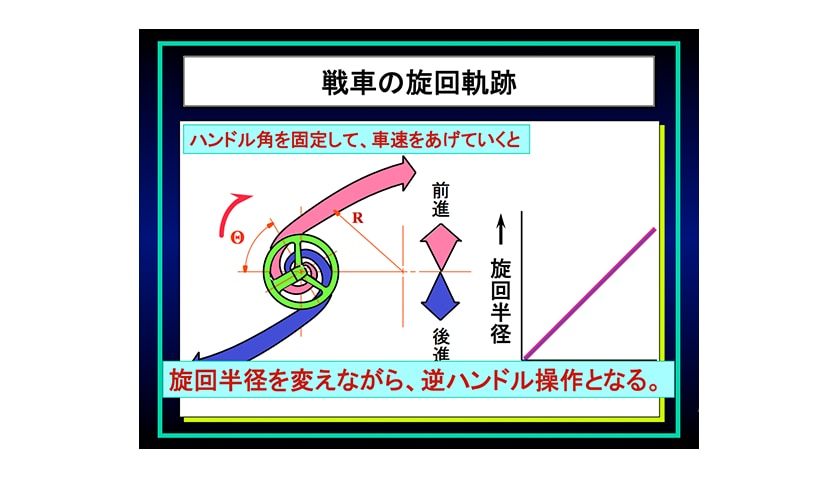
こうして、「クラッチ&ブレーキ方式」の弱点を克服するために、「強制デファレンシャル方式」と「円錐式ステアリングリンク」を組み合わせ、丸ハンドルFDS(フルタイムドライブシステム)と称し(資料5)、平成10年から商品化している。
また、
- 車速を超低速から高速までノークラッチで 無段階に変速が可能
- ゆるやかな旋回から スピンターンまで、簡単・スムーズに操作が可能
- 湿田圃場作業でも、優れた旋回と走行が可能
といった三つの特長を生かし、コンバインのシリーズ展開を行うと同時にトラクタや他の作業機に搭載し、コア技術として確立させたのである。今回は、その「強制デファレンシャル方式」を「クラッチ&ブレーキ方式」と比較しながら紹介するとともに、ハンドル化したステアリング操作方式とのマッチング構造について報告する。
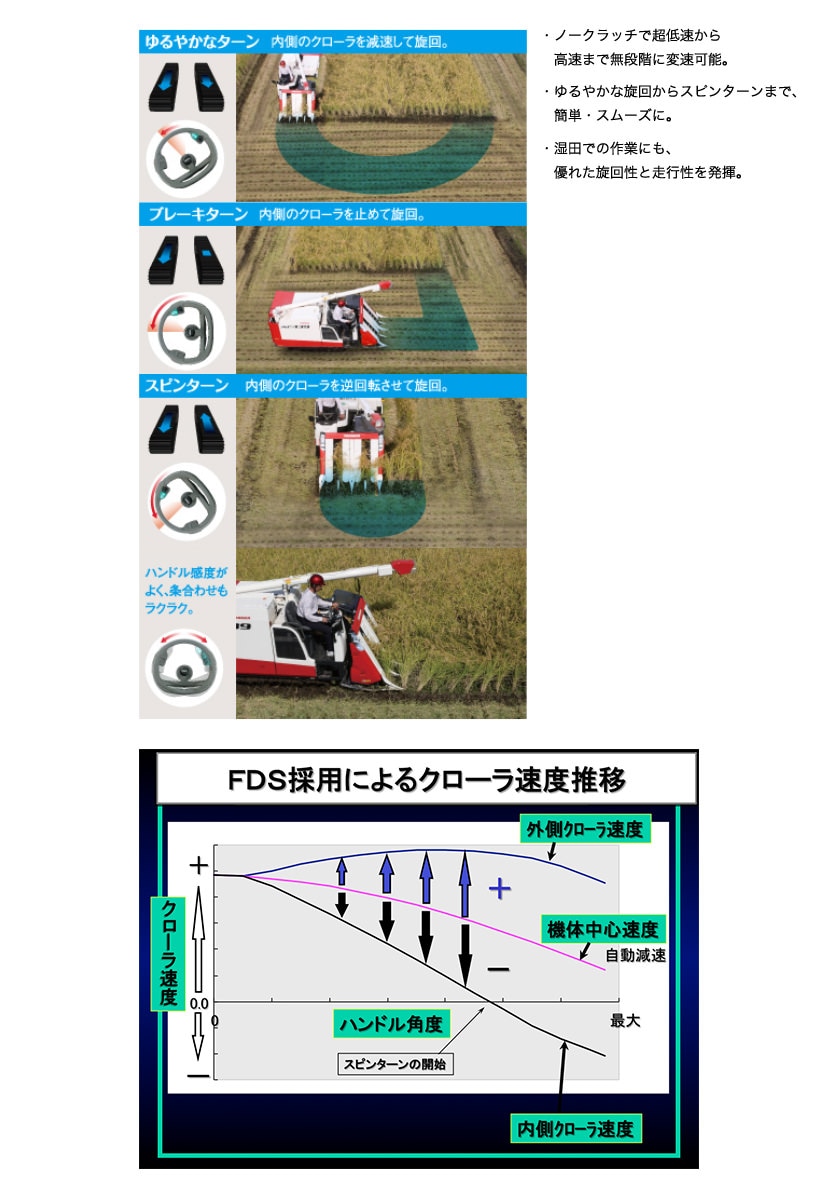
操舵システムに採用されているトランスミッション
1.「クラッチ&ブレーキ方式」の特徴
直進状態では左右両側に動力を伝達しているが、旋回状態では旋回内側のクラッチを切り動力を絶つことで車両を緩旋回させ、作物の植え付け状態に追従するように車両をコントロールする操舵方式である。また圃場の端など急旋回が必要な場合は、旋回内側の駆動輪にブレーキをかけることにより旋回する操舵方式である。(資料6)
そのため「旋回性能」・「湿田走破性能」・「耐久性能」において、次に示す3つの弱点を有している。

- 旋回性能
クラッチの切れるタイミングやブレーキの効き具合により旋回半径が異なるため、ギクシャクとした旋回になり、滑らかかつ正確な旋回ができない。
- 湿田走破性能
旋回時、内側クローラの動力が失われて片側駆動となるために、湿田条件下では推進力が低下し、状況によっては走行不能となる。
- 耐久性能
ブレーキに「摩擦板」を採用しているため、その摩耗度合によってブレーキ性能が左右され、安定した旋回を維持しづらい。
2.「強制デファレンシャル方式」の特徴
まず、「旋回性能」と関係の深い旋回機構について述べる。
左右の駆動がつながっている状態で、ギクシャクせず滑らかに旋回する機構としては、車の差動(デファレンシャル)ギヤがある。車は旋回時、後方車輪の旋回内側が遅く、外側が速くなっている。差動ギヤは、この時発生する左右の車輪の回転差を吸収する働きをしている。一方、「強制デファレンシャル方式」は、このデファレンシャルギヤを逆に強制的に回して左右のクローラに速度差を与えて旋回する方式で、この機構によって旋回性能を大きく向上させることが可能となった。また、車と違う部分としては、左右に遊星ギヤを配置することで強制動力を与えるHSTを固定した状態で差動させる方式としている点である。(資料7)
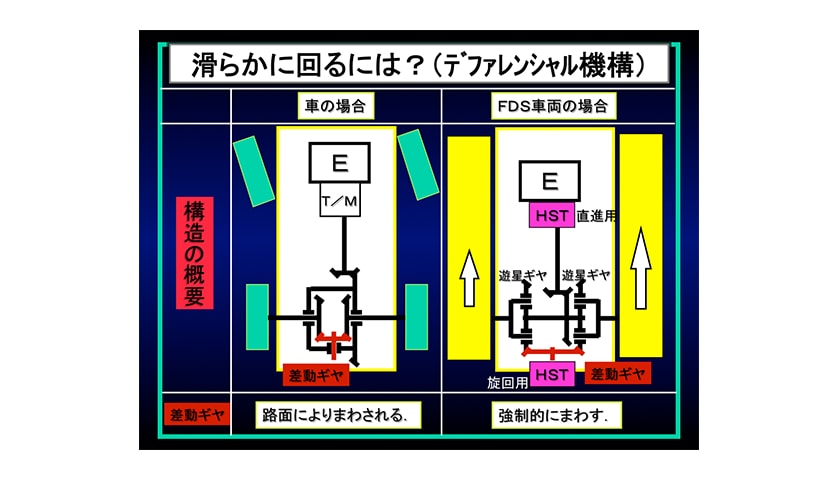
次に、「湿田走破性能」と最も関係の深い動力伝達について述べる。(資料8)
ポンプ1とモータ1で構成されるHSTが本機の前後進を行う。
モータ1の出力は、左右に配置されたプラネタリギヤのサンギヤへと入力される。
ポンプ2とモータ2で構成されるHSTが本機の旋回動作を行う。
モータ2の出力は二手に分かれ、一方がプラネタリギヤのリングギヤに直接入力され、もう一方が逆転ギヤを介してリングギヤへと入力されていく。モータ2が回転することにより、お互いのリングギヤは逆方向へ回転することになる。
サンギヤとリングギヤの合成動力が、プラネタリキャリアにより左右のスプロケットへと伝達される。
直進するときは、モータ2の回転を停止することにより確実に直進する。
旋回するときは、モータ2の回転を徐々にあげていくことにより滑らかに旋回する。
さらにこのミッションは動力伝達経路の中にクラッチをもっていないため、どの様な条件下においても左右のクローラへの動力を絶たないフルタイムドライブを実現したミッションといえる。
また、「耐久性能」を左右する摩擦板が存在しないため、高耐久を実現できた。
つまり「強制デファレンシャル方式」の採用によって、「クラッチ&ブレーキ方式」の弱点である「旋回性能」・「湿田走破性能」・「耐久性能」を向上させることができた。
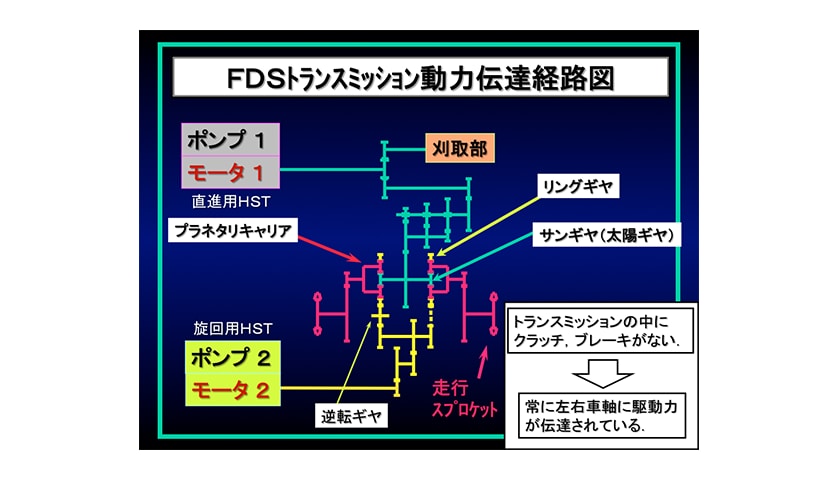
ステアリング操作方式
1.「丸ハンドル」円錐式ステアリングリンク
前にも述べたように「フルタイムドライブシステム」を開発した当時目指した操作感覚は、「乗用車感覚の操作」である。
乗用車感覚の操作を具体的に列記すると、
- ハンドルの切れ角に応じて思い通り旋回ができる。
- ハンドルが直進位置ならば直進する。ふらふらしない。
- 前進状態でハンドルを右に切ると右に旋回する。
- 後進状態でハンドルを右に切ると右に旋回する。
- ハンドル切れ角度が一定ならば、車速の変化にかかわらず旋回半径は常に一定
となる。どの項目も乗用車にとっては当たり前のことである。
ただし、前述の操舵システムである「強制デファレンシャル方式」と「単純なステアリングリンク」との組合せでは、
- 前進後進で逆ハンドル操作になる。
- スピンターンさせづらい。
- 車速の変化にかかわらず旋回半径を一定にできない。
といった状態に陥ってしまう。
この問題を解消するために弊社で開発されたのが「円錐式ステアリングリンク」である。
ステアリングハンドルと主変速レバーの出力を一旦円錐リンク機構と呼んでいるメカニカルな演算機構の中に入れ込み、そこから直進用及び旋回用HSTの操作レバーに入力している。(資料9)
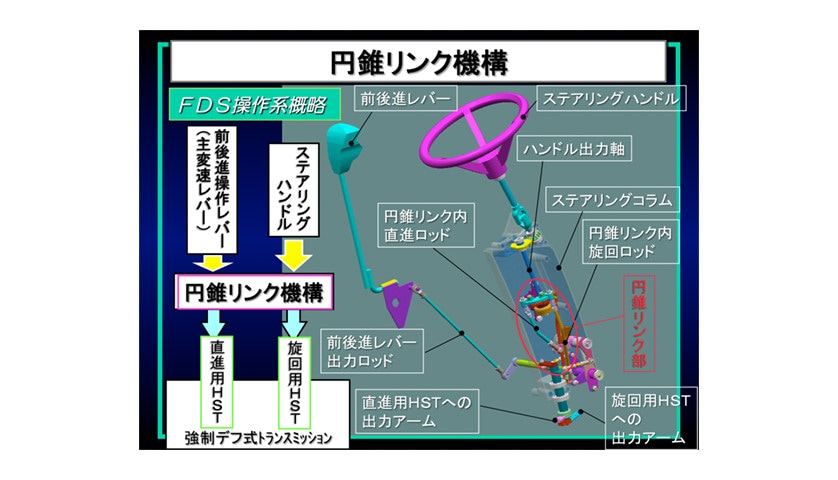
「円錐式ステアリングリンク」(前提模式図)(資料10)は、円錐の底円に位相差90度をつけて直進用ロッドと旋回用ロッドの端点が位置する。そして、両ロッドの他方の端点は、大小二つの円錐の頂点に位置する。
各直進用旋回用円錐の頂点の動きが、直進用HST・旋回用HSTの操作アームの位置となる。また、前後進用レバーの回動角度が円錐底面の傾きに比例する。さらに、ハンドルの切れ角度が円錐の底円の回動角度に比例する。図は、機体が停止している状態を示している。機体停止状態(上図)から、ハンドルを右方向へ回していくと下図の様になる。この時、円錐の頂点から底円までの距離は常に等しいため、直進用HSTも旋回用HSTも操作アームが動かず回転が発生しない。つまり、本機は停止し続けることになる。(資料11)
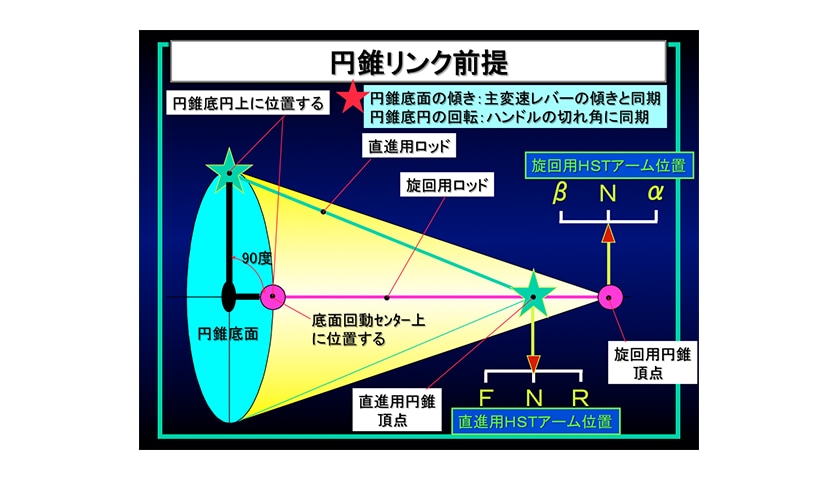

次に機体停止状態から前後進レバーを前進方向へ倒していくと上図の様になる。この時直進用HSTの操作アームは「F」側へ動く。しかし旋回用HSTの操作アームは、旋回用ロッドの端点が底面の回動中心ライン上に位置しているため動かない。つまり、前進方向に直進状態にある事になる。(資料12)
その状態からハンドルを右へ切っていくと下図の様に直進用HST操作アームは減速方向へ動き、旋回用HST操作アームはα方向へと動く。つまりハンドルを切るにしたがって車速が自動減速されながら右方向へ旋回していくことになる。この時、旋回用HST操作アームの移動方向はα側である。
後進状態では、上図の様になり前進時と同様旋回用HSTの操作アームは動かないため、後進方向へ直進状態になる。この後進状態から前進時と同様にハンドルを右方向へ切ると、直進用HSTの操作アームはやはり自動減速される。そして旋回用HSTの操作アームは前進時の逆のβ方向へと動く。 (資料13)
前進時と後進時旋回用HSTの操作が逆転している。この現象から逆ハンドル現象が解消されていることがわかる。
このように、「丸ハンドル」円錐式ステアリングリンクは、「円錐の頂点から底円までの距離は等しい」といういたって単純な原理を利用する事により乗用車感覚の操作を実現できた。また、全てをメカニカルに構成し前述「前進後進で逆ハンドル操作になる」、「スピンターンさせづらい」、「車速の変化にかかわらず旋回半径を一定にできない」の3つの問題を解決している。この技術は世界に類を見ないヤンマー独自技術である。
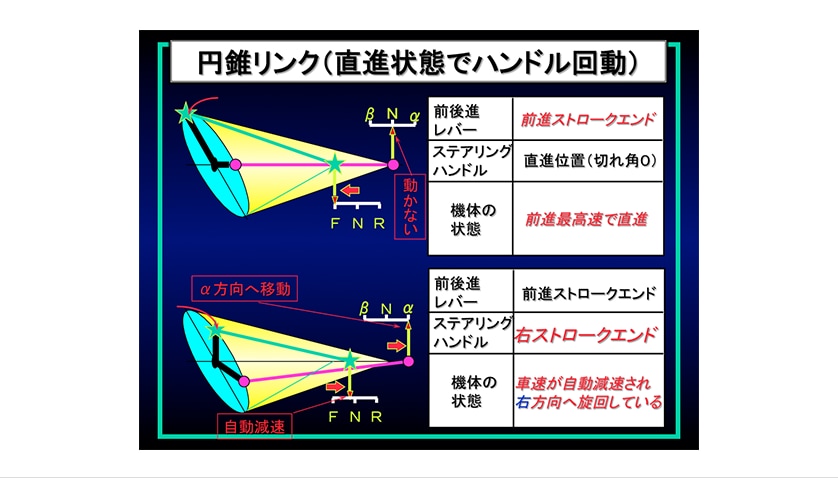
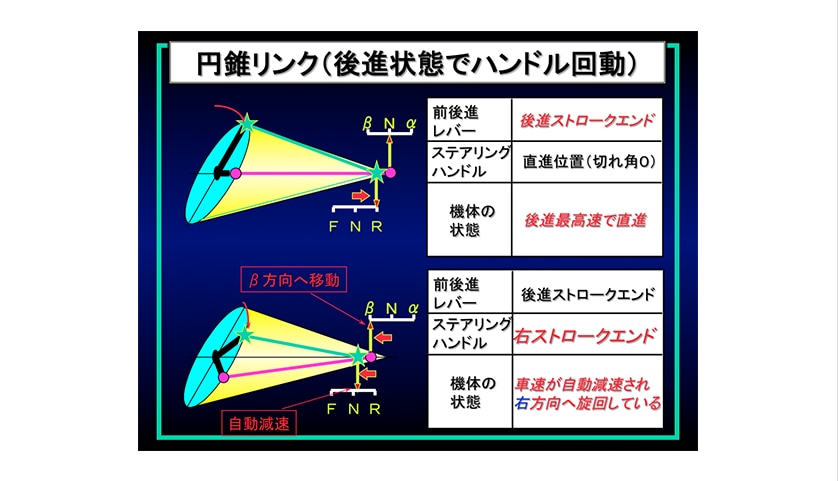
2.リングカム式ステアリングリンク
フルタイムドライブシステムの商品化以降、「円錐式ステアリングリンク」は、その部品点数の多さからさらなるコストダウンが要求されていた。また、調整箇所の多さから信頼性の向上も要求されていた。これに対して部品点数の削減を実施し、平成23年に商品化されたのが「リングカム式ステアリングリンク」である。(資料14)
この方式は、円錐の回転軸方向に全体を圧縮していくと円盤(リング)になるという発想から生まれたもので、カムを利用して構成したステアリングリンクである。「円錐式ステアリングリンク」に比べコスト低減を実現したほか、各部位のアソビを詰めることができ、操作フィーリングも向上した。また、全体をコンパクトなケースに収めることができたため、足もとがすっきりし居住性が向上した。さらに調整箇所も格段に減少したため、信頼性も向上した。
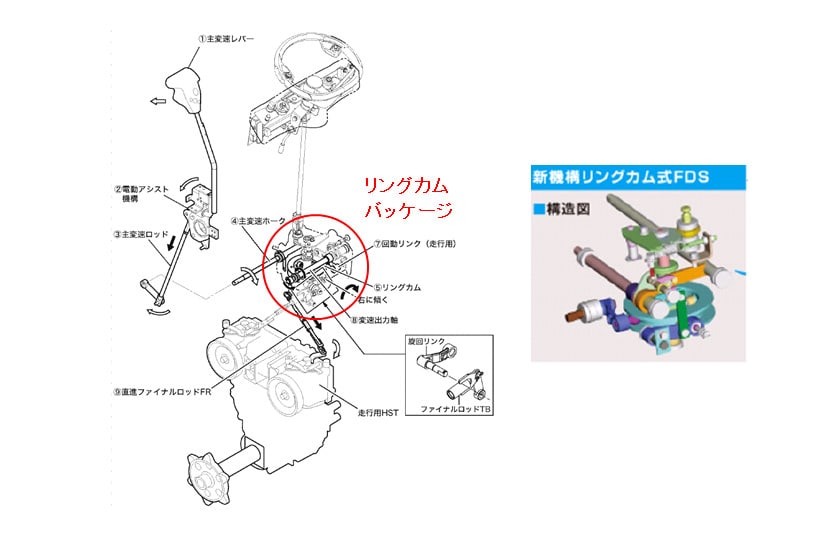
3.ステア・バイ・ワイヤ(Steer by Wire)式
ヤンマーが平成24年に商品化したフラッグシップコンバインには、「超高速作業」・「長時間作業」といった国内市場顧客の高度な要求に応えるべく、電子制御化(リンクレス化)したステアリング操作方式が搭載されている。この方式では、操作フィーリングのカスタマイズ(切り替え)を実現可能にしたほか、操作力の低減も実現している。また、ステアリングとミッションをつないでいたリンクを廃止することで、キャビンの穴を塞ぐことが可能となり防音防塵性が向上した。(資料15)
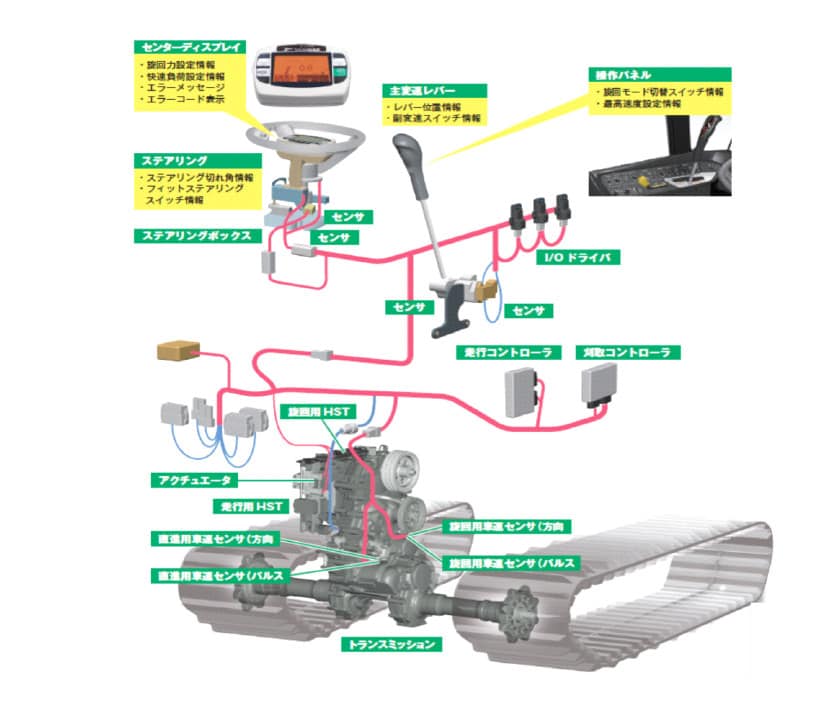
おわりに
「麦」を主に収穫するために欧米で発達してきた普通型コンバインは、日本の「稲」の収穫には適応性が低かったため、昭和41年日本特有の収穫機として自脱型コンバインが開発された。その後エネルギー効率の良い脱穀方式の改良により、作業速度が高速化していった。それにともない走行部・操舵系が改善され、今回の操舵システムがヤンマー独自のコア技術として確立し、商品化することができた。
今後も収穫技術の発展に伴い、進化を遂げるコンバインの新技術に挑戦していく所存である。
著者
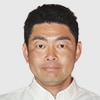