Fundamental Technology Research Center
Research & Development Center
Innovation & Technology Division
YANAMR HOLDINGS CO., LTD.
YANMAR Technical Review
Topic 2: A Study on Combustion Improvement in Dual-fuel Engine for Biogas Applications
Abstract
As the biogas produced by methane fermentation contains a high fraction of carbon dioxide, it is necessary to understand the effect this carbon dioxide has on the ignition and combustion characteristics of diesel pilot-ignited dual-fuel natural gas engines when they are run primarily on biogas. This study admixed carbon dioxide into the engine intake mixture to investigate its effect on combustion characteristics and engine performance parameters such as thermal efficiency. The article also discussed measures for improving combustion and engine performance. This work achieved brake thermal efficiency equivalent to that of the original dual-fuel engine fueled with natural gas even when carbon dioxide was present in the same ratio as in actual biogas.
This article also describes a facility that has installed the biogas dual-fuel engine that was developed using the results of this study.
1. Introduction
While biofuel contains carbon compounds and therefore releases carbon dioxide (CO2) when burned, it is deemed to be carbon-neutral because this carbon is derived from living organisms in the first place and so its release only returns it to nature. Biofuel is seen as playing an important role in reducing greenhouse gas (GHG) emissions, not least because its properties are closer to those of fossil fuels than is the case for other carbon-neutral fuels such as hydrogen or ammonia, which do not themselves contain carbon. While the fact that it is made from living organisms means that ensuring adequate supplies of biogas poses a problem, the use of biogas made from methane produced by fermenting materials such as sewage sludge or food waste that do not compete with food could provide a valuable resource for addressing environmental problems.
Yanmar has developed a dual-fuel (DF) engine that can run on biogas. This article explains how combustion techniques were developed for this engine and describes an actual installation.
2. Challenges for Engines Running on Biogas and Features of DF Engines
Table 1 lists the typical ranges of composition for biogas made by methane fermentation. The main components of biogas are methane (CH4) and CO2. This high concentration of unreactive CO2 gas is what differentiates biogas from conventional town gas. The variability of biogas composition also means that its per-unit-volume calorific value and stoichiometric air quantity are likewise variable. These fluctuations have a significant influence on engine operating conditions. Accordingly, if biogas is to be used as a fuel for engines, it will be important to determine how much influence this unreactive gas has on combustion and to set appropriate operating conditions.
Table 1 Main Constituents of Biogas from Methane Fermentation
Biogas | Town gas (13A) | |
---|---|---|
CH4 [vol.%] | 50.0 to 65.0 | 89.6 |
Other hydrocarbons (C2H6, C3H8, etc.) [vol.%] | 10.4 | |
CO2 [vol.%] | 35.0 to 50.0 | - |
N2, O2, H2 [vol.%] | 0.2 or less | - |
Lower calorific value [MJ/m3N] | 17.9 to 22.3 | 49.4 |
Stoichiometric air [m3N/m3N] | 4.76 to 6.19 | 16.8 |
In the case of spark-ignition engines in particular, which have low ignition energy, there is the potential for problems such as when the variability of gas composition exceeds what the engine control is able to cope with, which in the worst case could result in the engine not being able to start. Use of DF engines is one way to resolve problems like this.
Fig. 1 shows a diagram of a DF engine. A key feature is that it is equipped with separate fuel systems for diesel and gas. The engine can run on diesel only (diesel mode) or with gas as its main fuel (gas mode), and is able to switch between these two modes as required. As a small quantity of diesel is injected to promote ignition when running in gas mode, the engine is equipped with a micro pilot diesel injector exclusively for this purpose. The engine can operate reliably despite using biogas with variable fuel composition by running in diesel mode in situations where combustion is unsteady, such as when starting or cold, and then switching to gas mode once it is running steady.
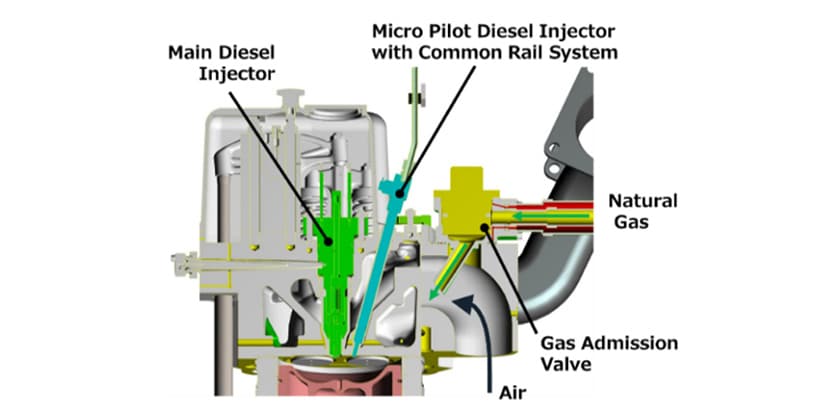
3. Achieving Appropriate Biogas Combustion in Dual-fuel Engine
3-1. Test Apparatus
The development of a DF engine that can run on biogas started with preliminary experiments that simulated the use of biogas using an experimental single-cylinder engine. Being only a single-cylinder engine meant the device was small, making it ideal for this sort of preliminary testing as setting up and conducting tests could be completed quickly.
3-2. Study of Influence of CO2 on Combustion
Fig. 2 shows the influence that the CO2 in biogas has on engine combustion. Fig. 2(a) shows how thermal efficiency falls as the proportion of CO2 rises. Similarly, Fig. 2(b) plots cylinder pressure and combustion for different levels of CO2, showing how the post-ignition combustion rate slows as the proportion of CO2 rises. These results indicate that the CO2 in biogas will tend to slow the combustion rate and reduce the engine’s thermal efficiency.
One way to address a slower combustion rate in a spark-ignition engine is to advance the ignition timing. When the DF engine is operating in gas mode, a small amount of diesel (pilot fuel) is injected to achieve ignition. Accordingly, Yanmar investigated the effects of varying the pilot fuel injection timing. Fig. 3 shows the experimental results. Fig. 3(a) shows that there is little variation in the injection timing that delivers maximum thermal efficiency, regardless of whether or not CO2 is present. Fig. 3(b) shows the relationship between the pilot fuel injection timing and the crank angle at which different mass fraction burned (MFB) percentages are achieved for a fuel with 36% CO2. Here, MFB10, MFB50, and MFB90 represent the crank angles at which 10%, 50%, and 90% respectively of the fuel has burned. As MFB10 indicates the start of combustion, a low value indicates that ignition is fast. If the pilot fuel injection timing is advanced beyond a certain timing, MFB10 begins to rise and this can be interpreted as ignition getting slower. The likely reason is that, if the injection timing is advanced too much, not only will conditions inside the cylinder not reach the pressure and temperature at which the pilot fuel will self-ignite, but the pilot fuel will also become leaner through mixing with the surrounding air, further increasing the pressure and temperature required for self-ignition. That is, advancing the timing may instead delay the start of combustion. These results indicate that the slow combustion rate caused by the presence of CO2 cannot be improved by changes to the pilot fuel injection timing and that some other means of improving combustion is needed.
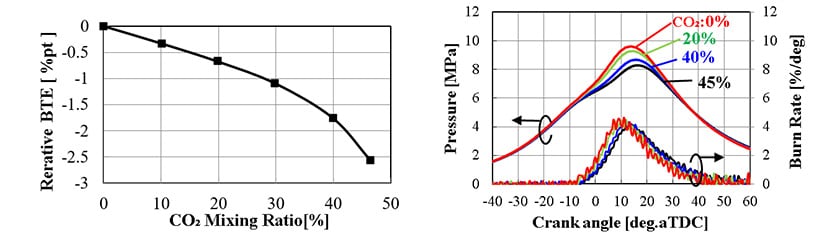
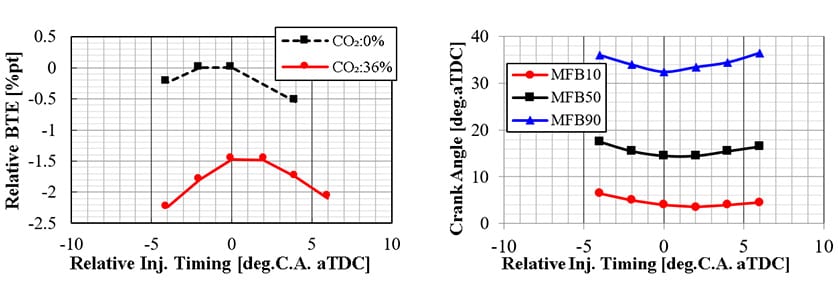
3-3. Combustion Improvement
Given the above result, Yanmar set out to investigate other ways of improving combustion. Separate testing had found that increasing the charge air temperature was especially beneficial for combustion. (More information about this testing is provided in the references.)
Fig. 4 shows how the charge air temperature influences engine thermal efficiency (for 45% CO2). The performance relative to the standard charge air temperature was evaluated for temperature increases of +10, +15, and +20°C. The results indicated that increasing the charge air temperature made advancing the pilot fuel injection timing more effective, with thermal efficiency similar to that of natural gas being achieved at +20°C. This is believed to be due to the higher charge air temperature raising the temperature in the cylinder, leading to earlier diesel ignition.
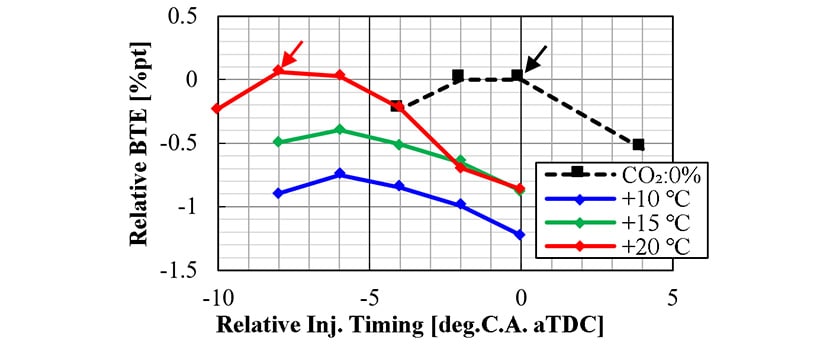
4. Example Application: Mikasagawa Purification Center
This section describes the installation of a 6EY26LDF, Yanmar’s first dual-fuel engine intended to run on biogas.
The Mikasagawa Purification Center in Fukuoka Prefecture commissioned a digester gas generation system in April 2023. As indicated by the overview in Fig. 5, the center uses DF engines to generate electricity from the digester gas produced by fermentation of sludge from the sewage treatment process. The facility is equipped with two 990-kW 6EY26LDF engines (see Fig. 6) that it is estimated will generate approximately 6,000 MWh of electricity each year, enough to power around 2,000 homes. This amount of energy equates to an approximate 2,292-ton reduction in CO2 emissions.
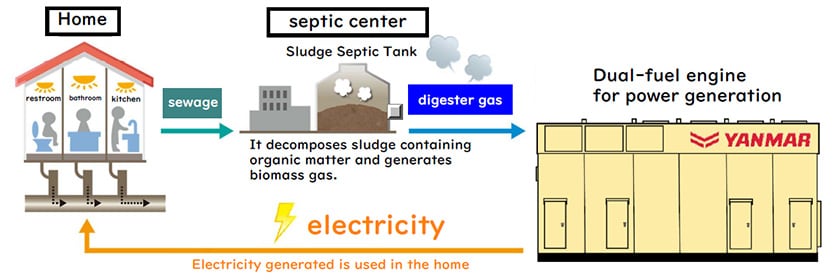

Fig. 7 shows an example operating pattern for the 6EY26LDF engines at the Mikasagawa Purification Center. After running briefly in diesel mode when starting, they switch to gas mode once the requisite conditions are satisfied. This ensures reliable engine starting, avoiding problems caused by the variability of gas composition. As the electric power generated by this system can be sold under the feed-in tariff (FIT) scheme set up by the Act on Special Measures Concerning Procurement of Electricity from Renewable Energy Sources by Electricity Utilities, it is configured to only supply electricity to the grid when running in gas mode.

5. Conclusions
This article has described the development of a dual-fuel engine that can run on biogas. By taking advantage of the features of dual-fuel engines, Yanmar has overcome the challenges of running on biogas and succeeded in supplying its customers with highly reliable systems. As the need to reduce GHG emissions is set to make technologies for using biogas ever more important, Yanmar intends to continue striving relentlessly to deliver products that are a close fit with customer requirements.
6. References
- (1)Yusuke Honda, Kazuteru Toshinaga, Hirofumi Yukawa, Kazuo Migita, A Study on Combustion Improvement in Dual-Fuel Engine for Biogas Applications, JSAE Internal Combustion Engine Symposium, 20214873, (2021) in Japanese.
-IMPORTANT-
The original technical report is written in Japanese.
This document was translated by Innovation & Technology Division, Technology Strategy Division.
Author
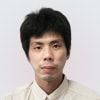
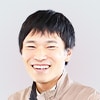
Fundamental Technology Research Center
Research & Development Center
Innovation & Technology Division
YANAMR HOLDINGS CO., LTD.
Kazuki Toshinaga

Large Engine Technology Department
Engine Development Division
YANMAR POWER TECHNOLOGY CO., LTD.
Hirofumi Yukawa
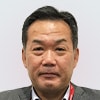
Engineering Division
YANMAR ENERGY SYSTEM CO., LTD.