Development Division
Large Power Products Business
YANMAR POWER TECHNOLOGY CO., LTD.
YANMAR Technical Review
Introduction of Dual-Fuel Engine Second Report: Efforts for a Decarbonized Society
Abstract
The shipping industry has been studying alternative fuels and technologies able to replace petroleum-based fuels as part of its efforts toward decarbonization. In the transitional period to 'carbon neutrality', LNG is a leading contender among such alternative fuels, already used in an increasing number of onboard systems and the subject of ongoing technology development. Yanmar has been developing dual-fuel engines able to run on both gas and diesel fuel. The first such dual-fuel engine, the 6EY26DF, was described in an earlier article in the April 2019 edition. This follow-up report describes subsequent technology developments and the work being done to address its technical challenges.
1.Introduction
The shipping industry is stepping up its efforts to achieve carbon neutrality. The 72nd session of the Marine Environment Protection Committee (MEPC) of the International Maritime Organization (IMO) held in 2018 approved a target of halving total annual greenhouse gas (GHG) emissions by 2050 compared to 2008, with even more ambitious targets now under discussion. In Japan, meanwhile, a roadmap for achieving zero emissions in international shipping was formulated in March 2020. Alongside these developments, work is also being done on the use of new forms of energy such as hydrogen, ammonia, and biomethanol that can replace the fossil fuels currently burned in marine engines. Although not carbon-neutral, liquified natural gas (LNG) and other such gaseous fuels have lower emissions than traditional fuels in terms not only of CO2, but also of atmospheric pollutants such as nitrogen oxides (NOX) and particulate matter (PM). As technology development is well advanced and ready for immediate deployment, such fuels are seen as an alternative form of energy for use during the transition to the newer fuels referred to above.
Yanmar Power Technology has developed a dual-fuel engine that can run on gas supplied from LNG as well as on diesel. The engine was described in an earlier article published in YANMAR Technical Review in 2019(1). This follow-up article provides an update on the technology of the dual fuel engine and the work being done to address its technical challenges.
2.Dual-Fuel Engine Mixed Combustion Mode Operation
The high degree of variability in gas heat content and pressure associated with the LNG bunkering process*1 is the reason why natural gas cannot generally be used as fuel for a ship’s engine. Instead it is burned in a gas combustion unit (GCU). The Yanmar dual-fuel engine is able to run in gas mode, diesel mode, and also in a mixed combustion mode in which the supplies of gas and diesel are regulated to allow use of both at once. That is, the engine is controlled in a way that allows it to make use of gas as a fuel even under conditions where it is difficult to utilize.
Fig. 1 shows the relative percentages of gas and diesel fuel supplied to the engine when running in mixed combustion mode. As the diesel injection amount is used to regulate the engine speed, reliable operation at a steady speed can be maintained even if the heat content or pressure of the gas varies.

- *1Bunkering refers to the filling of a ship’s fuel tanks with fuel. LNG bunkering requires that supply lines be purged with an inert gas before and after supplying the LNG to prevent it from catching fire. This is why the bunkering process tends to be associated with a lot of variability in the gas heat content and pressure. (Fig. 2 shows an example of the truck-to-ship bunkering of LNG.)

3.Technical Challenges of Dual-Fuel Engine
Using LNG fuel in an engine significantly reduces its emissions(1). However, if the objective is to reduce GHG emissions, then it is essential that the amount of methane slip be minimized. Methane slip refers to methane from the LNG that ends up being released into the atmosphere unburned. This is important because the global warming potential of methane is 25 or more times higher than CO2.
To achieve high power and low NOX emissions, gas engines are typically lean burning, which is achieved by appropriate control of the fuel-air mixture (the ratio of air and fuel injected into the engine cylinder). This also applies to the dual-fuel engine. As shown in Fig. 3, while lean burning delivers a steady, high level of power together with lower NOX emissions due to combustion happening at a lower temperature, this comes at the cost of more unburned gas, in other words, increased methane slip. To reduce methane slip without compromising engine performance, Yanmar has been working both on design and combustion improvements in the engine itself and on catalyst-based exhaust aftertreatment systems.

3.1 Engine Improvements
This section looks first at the improvements made to the engine itself. There are two mechanisms in particular that make premixed lean burning prone to methane slip, as follows.
- 1)Valve overlap (when both inlet and outlet valves are open at the same time) allows gas fuel supplied to the air inlet pipe to blow out to the exhaust rather than remaining in the cylinder.
- 2)Residual fuel-air mixture not burned inside the cylinder is exhausted as unburned gas
In the former case 1) of gas fuel being blown out of the cylinder, what matters is how the intake process can trap the gas fuel supplied to the air inlet pipe. This in turn requires improvements to the intake and exhaust timings, and to the supply timing and quantity of gas fuel.
Yanmar used analytical techniques to study the intake and exhaust timings and the timing, quantity, and method of gas fuel supply. Fig. 4 shows an example of a study using computational fluid dynamics software to analyze gas supply to the cylinder. The study was used to optimize the supply of gas and the geometry of the parts involved. Similarly, Fig. 5 shows example results for the predicted and measured values of total hydrocarbon concentration (THC) (a measure of methane slip) and engine performance for different gas supply timings. These results demonstrate how Yanmar’s design capabilities and analytical expertise enable performance to be predicted with high accuracy.


To minimize the exhaust of unburned gas in the second case 2), what matters is to promote combustion and to keep regions inside the cylinder where combustion does not occur to a minimum.
These latter regions are called dead volumes. One is the crevice between the piston top land and cylinder liner. It is known from past experimentation that the amount of unburned gas is strongly correlated with the volume of this crevice. In the dual-fuel engine, the crevice volume was minimized by adopting a high-top configuration in which the top ring is positioned as close as possible to the top of the piston, which has a flat geometry.

Yanmar has also been studying multi-stage injection as a means of promoting the combustion reaction(2). This has succeeded in both boosting thermal efficiency and reducing unburned hydrocarbons by using multi-stage injection under certain load conditions.
3.2 Improvements of Catalyst-based Exhaust Aftertreatment Systems
Yanmar is participating in the Development of Next-Generation Vessels Project(3) sponsored by the Green Innovation Fund. One initiative being undertaken as part of this project is entitled “Development of Methane Slip Reduction Technology from LNG Fueled Vessels by Improving Catalysts and Engines”. This will see Yanmar working with partner companies to reduce the environmental impact of LNG-fueled ships by delivering a 70% or more reduction in methane slip by 2026, achieving this through a combination of engine improvements and the use of methane oxidation catalysts.
4.Conclusions
This article is a follow-up to an article that appeared in the 2019 spring edition of YANMAR Technical Review, providing an update on the technology of the dual-fuel engine and the work being done to address its technical challenges. It is anticipated that greater use will be made of LNG in the future as part of efforts toward decarbonization. Yanmar intends to persevere with technology development, developing the dual-fuel engine to deliver high levels of both engine and environmental performance.
Building on the foundation of the resulting technology, Yanmar also intends to continue with research and development aimed at realizing new power sources that can lead the way to carbon neutrality.
References
- (1)Katsuhiro Nishimura, Development of 6EY26DF Dual-Fuel Engine: Compliant with IMO Tier 3, YANMAR Technical Review, April 3, 2019
- (2)K. Toshinaga, et al., Advanced Combustion Strategy for Medium-Speed Dual-Fuel Engine, 2019-262, CIMAC CONGRESS 2019
- (3)Yanmar News Release, NEDO Selects Methane Slip Reduction Project for Next Generation Ship Development,
https://www.yanmar.com/jp/marinecommercial/news/2021/10/27/99019.html
-IMPORTANT-
The original technical report is written in Japanese.
This document was translated by Innovation & Technology Division, Technology Strategy Division.
Author
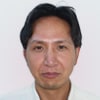