Development Division
YANMAR ENERGY SYSTEM CO.,LTD.
YANMAR Technical Review
Toward World-Leading Electrical Generation Efficiency: Development of EP420G Gas Engine Cogeneration System
Abstract
Gas engine cogeneration systems are a clean and energy-efficient means of burning city gas (made up mainly of natural gas) to generate electric power, with the excess heat being used for purposes such as heating water.
Yanmar Energy System Co., Ltd. supplies gas engine cogeneration systems with generation capacities ranging between 5 and 800 kW, with the recently developed EP420G achieving world-leading electrical generation efficiency for its output class of 42.6%. This contributes to the system offering outstanding life cycle value*1 to users. With recent years having seen a growing need for business continuity planning (BCP) measures that can deal with power outages caused by earthquakes or typhoons, the system also helps customers to improve resilience by serving as a distributed energy system.
- *1Life cycle value is the value that a product delivers to the customer over the course of its useful life. Yanmar strives to enhance life cycle value.
1.Introduction
The EPG series is a cogeneration system powered by a gas engine. Around 600 of these systems have been sold since they first became available in 2003, being used by customers as a resource for business continuity planning (BCP) and for saving energy. The new EP420G features world-leading electrical generation efficiency for its output class of 42.6%. This enables customers to achieve even higher levels of energy efficiency.
2.Overview of Gas Engine Cogeneration System and its Applications
Fig. 1 shows a diagram of a gas engine cogeneration system. These systems are a form of heat and power production that typically work by burning natural gas to generate electric power while also recovering and utilizing the heat that is produced in the process. While conventional thermal power generation can produce electric power equivalent to around 40% of the energy in the fuel it consumes, this increases to as much as 75% to 80% if gas cogeneration is installed close to sites of demand so that the electric power and heat can both be put to use. This enhanced energy efficiency delivers both better economics and lower CO2 emissions(1).
The Act for Establishing Energy Supply Resilience enacted by the Japanese Diet in 2020 called for measures to make the electricity system more resilient to natural disasters. As it uses city gas supplied at medium pressures, an energy source with a good ability to withstand earthquake damage, gas cogeneration can be used to build such disaster-resilient systems. When equipped with a black start capability, gas cogeneration can restore electricity to critical loads within 40 s in the event of an outage on the main grid, making it particularly well suited to forming part of robust business continuity plans(1), (2), (3).
Having kept customers supplied with electricity and heat through the grid outages caused by the Great East Japan Earthquake of 2011, gas cogeneration systems have come to be recognized as an extremely valuable form of energy supply to have on hand during major disasters(4), (5).

(from the website of Advanced Cogeneration and Energy Utilization Center Japan(1))
3.EP420G Overview
Fig. 2 shows an EP420G system and Table 1 lists its main specifications, with those of the previous EP370G model provided for comparison. The 42.6% electrical generation efficiency of the EP420G is world-leading for its output class and 1.6% higher than its previous model (see Fig. 3). Given the demand for a high level of electrical generation efficiency from customers who manage the hospitals and other commercial buildings where EPG series systems have been installed, the enhanced efficiency of the new model makes a major contribution to delivering higher life cycle value. BCP performance has also been enhanced as the new model is able to add load during a power outage in larger steps than previous systems.
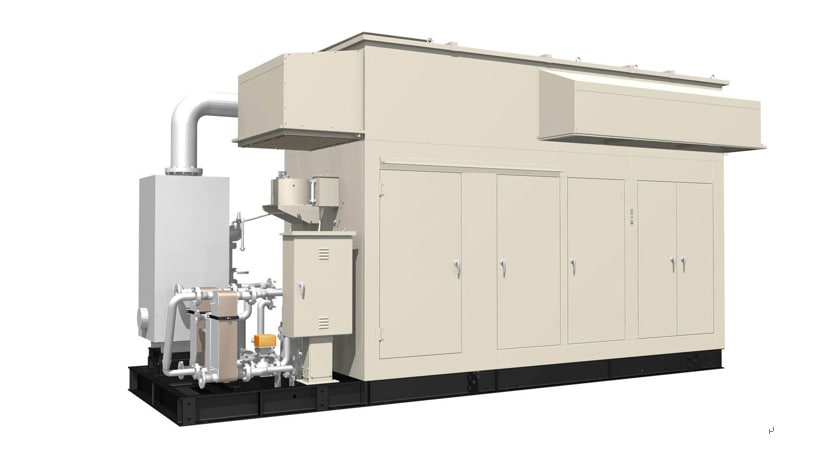
Table 1 Main Specifications of EP420G
Specification | Unit | EP420G | EP370G (previous model) | |
---|---|---|---|---|
Frequency | Hz | 50 | ||
Rated power | kW | 420 | 370 | |
Engine | - | AYG20L-ET | AYG20L-SE | |
Engine speed | min-1 | 1500 | ||
Electrical generation efficiency | % | 42.6 | 41.0 | |
Overall efficiency | Steam & hot water recovery model | % | 76.9 | 73.8 |
Hot water model | 78.4 | 75.0 | ||
Load step (percentage) | kW (%) | 126 (30) | 111 (30) | |
Noise | dB(A) | ≦75 | ||
NOX (O2=0%) | ppm | ≦200 (does not require NOX removal system) |
||
External dimensions of housing* (steam & hot water recovery model) |
Length × width × height | mm | 7,734×2,200×3,627 | 7,735×2,200×3,630 |
- *Excludes air intake hood
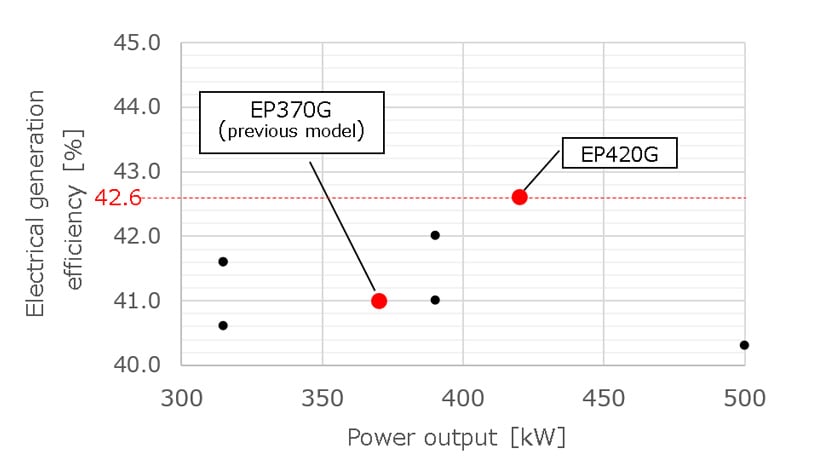
Fig. 3 Global Data on Gas Engine Electrical Generation Efficiency and Power Output(6)
4.Development of EP420G
4.1.Achieving high efficiency
The development of the EP420G engine used the previous EP370G engine as a base. Table 2 lists the techniques used to achieve high efficiency and Fig. 4 shows how well these worked. The result was an increase in electrical generation efficiency of 1.6% over the EP370G engine.
Table 2 Techniques Used to Achieve High Efficiency
Challenge | Solution |
---|---|
Higher efficiency | Higher power output |
Optimization of piston and auxiliary chamber geometry | |
Use of highly efficient turbocharger | |
Suppressing knocking | Revised intake and exhaust timings |
Use of turbocharger with high pressure ratio | |
Suppressing atmospheric pollutants | Combustion matching |
(1) Achieving high efficiency
Typically, the higher the power output of an engine and the greater its displacement, the higher its efficiency. As changing the displacement was not an option given that the new model was developed from an existing base, improvement in engine efficiency was achieved by increasing output. Combustion was also optimized by using a highly efficient turbocharger and by changes to the geometry of the piston combustion chamber and auxiliary chamber.
(2) Suppressing knocking
One of the challenges of increasing power output is that it makes the engine more prone to knocking. To suppress knocking, the Miller cycle was optimized to reduce the pressure and temperature inside the engine cylinder through changes to the intake and exhaust timings and the use of a turbocharger with a high pressure ratio.
(3) Suppressing atmospheric pollutants
The quantity of nitrogen oxide (NOX) emissions is corelated with engine efficiency as the conditions that achieve higher efficiency also result in increased emissions of this atmospheric pollutant. Because Japan’s Air Pollution Control Act and various local government regulations set standards for NOX emissions, the challenge is to find a way to improve engine efficiency while also minimizing these emissions. The target set for the EP420G was to be able to comply with the Tokyo regulations requiring emissions of 200 ppm (O2 = 0%) or less without using an NOX removal system, and the engine successfully achieved ultra-lean combustion over a wide range of operating conditions. As a result, so long as it is within the standard maintenance interval, the engine can stay below the NOX limit even when operated for long periods of time.
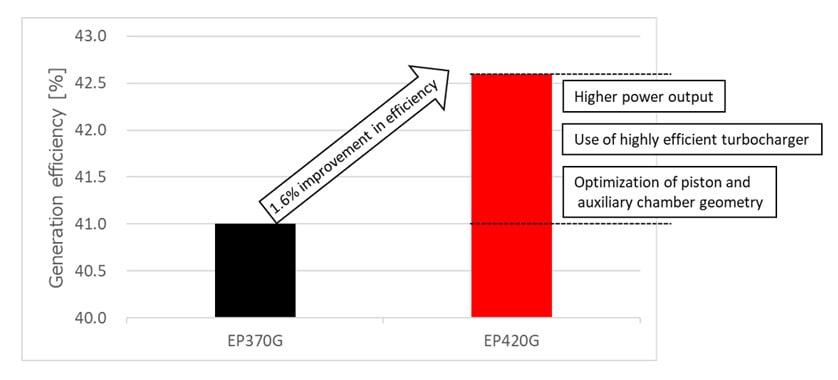
4.2.Improving BCP performance
4.2.1.Improvement of load step performance
The changes to the intake and exhaust timings and the use of a turbocharger with high pressure ratio, both adopted to improve engine efficiency, had the effect of making it more difficult for the system to handle load steps. This happens because applying a sudden load while the engine is idle degrades combustion performance due to a lack of air in the combustion chamber. Table 3 lists the ways in which this problem was overcome. As a result, load step performance was improved to the extent that the new engine can handle similar percentage load steps to the previous model.
Table 3 Techniques Used to Improve Load Step Performance
Improvement | Objective |
---|---|
Optimization of fuel injection control for combustion chamber and auxiliary chamber | Tune excess air ratio |
Ignition timing control | Adjust ignition timing to suit conditions when step change occurs and control to facilitate step change |
4.2.2.Use of remote monitoring to maintain good generator condition
As with previous models, the EP420G is supported by Yanmar’s Remote Energy Support System (RESS). Fig. 5 shows a sample remote monitoring screen. By supplying on-site service staff with operational information, this ensures reliable equipment operation both by enabling a faster response when failures occur and by establishing a system for identifying potential problems before they occur.
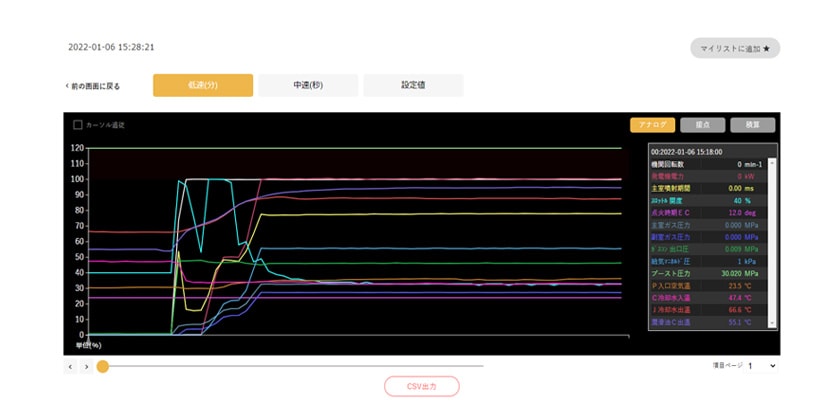
5.Conclusions
The EP420G was developed to achieve world-leading electrical generation efficiency, and has achieved an electrical generation efficiency of 42.6%. By providing customers with a highly efficient system, Yanmar is confident that the EP420G will help them save energy and improve life cycle value. Yanmar is also committed to ongoing product development that will enable it to supply solutions to the challenges customers face. The EP420G was jointly developed in partnership with Tokyo Gas Co., Ltd., Tokyo Gas Engineering Solutions Corporation, and Yanmar Power Technology Co., Ltd. The author would like to take this opportunity to thank everyone involved for the successful completion of the engine amid many unprecedented challenges.
References
- (1)Advanced Cogeneration and Energy Utilization Center Japan, Cogen Features (website in Japanese),
https://www.ace.or.jp/web/chp/chp_0030.html - (2)Agency for Natural Resources and Energy, Ministry of Economy, Legislative measures to improve power system resilience
Objectives of the revision of the energy-related Acts(website)
https://www.enecho.meti.go.jp/en/category/special/article/detail_159.html - (3)Advanced Cogeneration and Energy Utilization Center Japan, Potential for Cogeneration in National Resilience Policy: Role of Cogeneration in Revisions to Fundamental Plan for National Resilience (website in Japanese),
https://www.ace.or.jp/web/info_general/images/20190704111800_1.pdf - (4)Cabinet Secretariat, Sendai Microgrid Able to Continue Generation when Earthquakes Strike (website in Japanese),
https://www.cas.go.jp/jp/seisaku/kokudo_kyoujinka/minkan_torikumi/3_3/0304.pdf - (5)New Energy and Industrial Technology Development Organization, The Sendai Microgrid Operational Experience in the Aftermath of the Tohoku Earthquake: A Case Study,
https://www.nedo.go.jp/content/100516763.pdf - (6)Clean Energy Monthly, 2021 Data on Natural Gas Cogeneration Equipment, Japan Industrial Publishing p. 12–17 in Japanese
-IMPORTANT-
The original technical report is written in Japanese.
This document was translated by Innovation & Technology Division, Technology Strategy Division.
Author
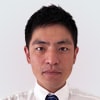