Advanced Development Division
Development Division
YANMAR AGRIBUSINESS CO., LTD.
YANMAR Technical Review
YR8D, A Auto-Rice Transplanter: Greater Labor Savings when Used with High-Density Seedlings
Abstract
Achieving straight rows when operating a rice transplanter depends on the skills and experience of the operator. Similarly, achieving equally spaced rows also requires high levels of concentration and can be fatiguing over long periods of operation.
Auto-rice transplanters use automatic steering to help keep the transplanter in a straight line during planting. By eliminating a task that would otherwise demand a high level of concentration, auto-rice transplanters both reduce fatigue and allow less experienced operators to plant seedlings at the same level as a skilled operator.
Moreover, even greater labor savings can be made when auto-rice transplanters are used together with Yanmar's high-density seedlings. Yanmar has been working on such developments in order to provide ever more customer satisfaction.
This report describes the features and technologies built into the YR8D, A auto-rice transplanter.
1. Introduction
As the shortage of agricultural workers worsens, there is a need for machinery that can work at the same level as a skilled operator regardless of who is operating it. Yanmar is developing such machinery for large-scale farming operations looking to expand and who are seeking high efficiency as well as reduced fatigue when working for extended periods of time, and also for rice farmers seeking to achieve a high level of transplanting work regardless of how much experience they have.
Following on from the Robot Tractor, the new auto-rice transplanter is the second in Yanmar's range of machinery marketed under the "SmartPilot" brand, used for models that incorporate automatic and autonomous driving technology. Yanmar has been working on developments that will provide ever more customer satisfaction by delivering even greater labor savings and higher efficiency. This has been achieved by incorporating technology developed for the Robot Tractor into the rice transplanter and using it in combination with Yanmar's high-density seedlings. This report describes these developments.
2. Product Overview
Yanmar markets its auto-rice transplanters (see Fig. 1) as the YR8D series. These are equipped with the same global navigation satellite system (GNSS) unit as the Robot Tractor (see Fig. 2). This unit was developed in-house by Yanmar, and works by using highly accurate real-time kinematic (RTK) positioning. The hardware and control algorithms from the Robot Tractor were used as a base and then fine-tuned to suit the requirements of a rice transplanter. The user interface also replicates the Robot Tractor by using a tablet (see Fig. 3) with the aim of achieving the same intuitive ease-of-use. This also provides consistency of operation across the different machines. The tablet display for rice transplanting was developed specifically for rice transplanting work to make it easier for users to understand.
The use of electric power steering (EPS) with fully electric steering actuators, adopted for the first time on this new model, provides highly accurate control for automatic steering as well as for automatic straight-line driving.
The auto-rice transplanter is operated by an onboard operator who is able to make changes in speed, and can be used in both automatic (automatic driving) and conventional manual driving modes.
To suit different conditions and preferences, two different modes of automatic driving are available: Linear Mode and Auto Mode.
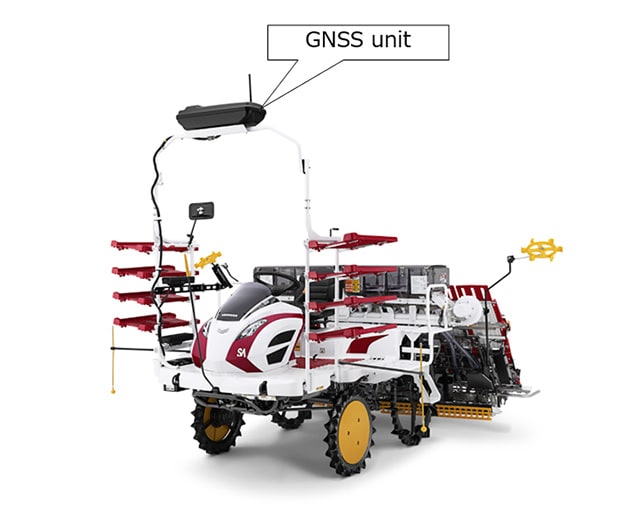
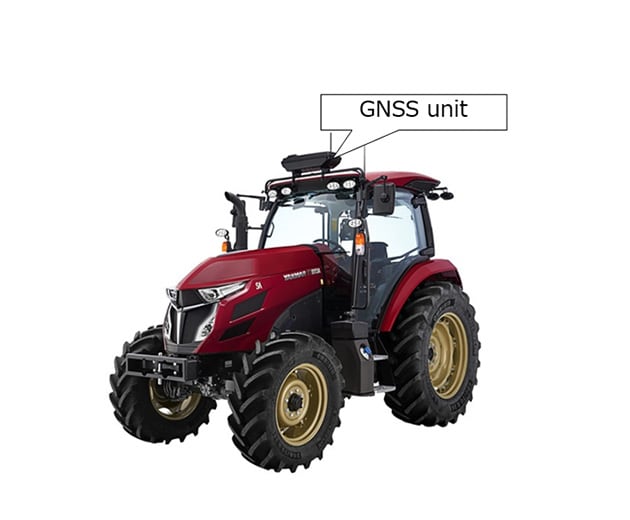
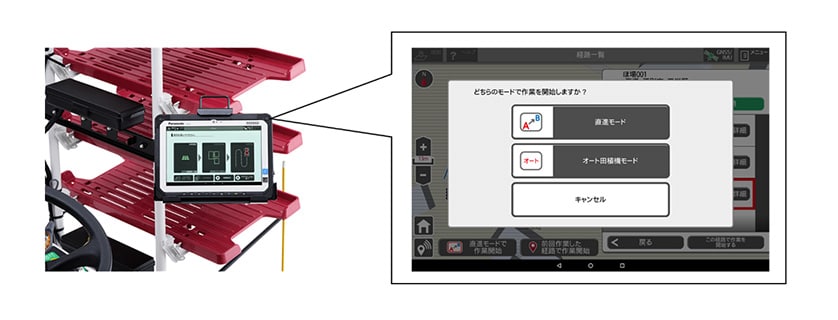
3. Features
3.1. Automatic Steering Modes
(1) Linear Mode
Linear Mode is an automatic steering function that tracks a reference line defined by specifying two points (points A and B in Fig. 4).
This mode works by defining the path to follow next in terms of a specified offset distance from the reference line and using automatic steering to follow this path. (For example, if the auto-rice transplanter is planting eight rows with a 30cm row spacing, the offset will be 30cm×8 = 2.4m. For a 33cm spacing it will be 33cm×8 = 2.64m.) The rice transplanter is turned manually at the end of each row, and the path-to-follow and actual vehicle position are plotted on the tablet in real time. Similarly, shading is used to indicate regions that have already been planted, providing an intuitive representation that can be understood by operators of all levels of experience (see Fig. 5).
In Linear Mode, the auto-rice transplanter generates multiple offset paths in advance relative to the reference line, and uses RTK positioning to minimize loss of reference line accuracy over time, thereby maintaining constant spacing between adjacent rows during planting. This should provide consistent growing conditions that will help boost crop yields.
To deal with cases whereby the operator wants to make temporary adjustments to the row spacing to suit field conditions, the rice transplanter is equipped with a "Path Shift" function that can commence automatic steering from any designated location (see Fig. 6).

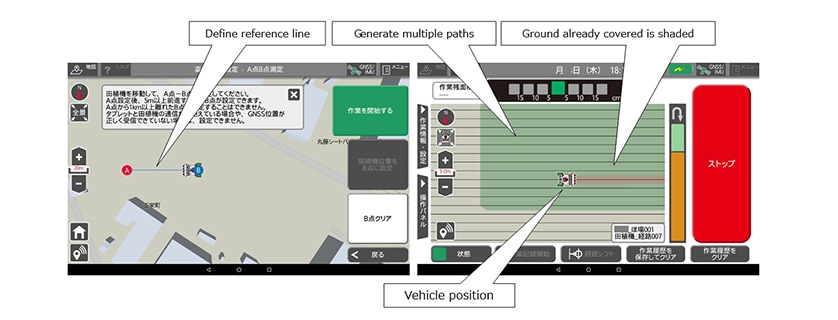
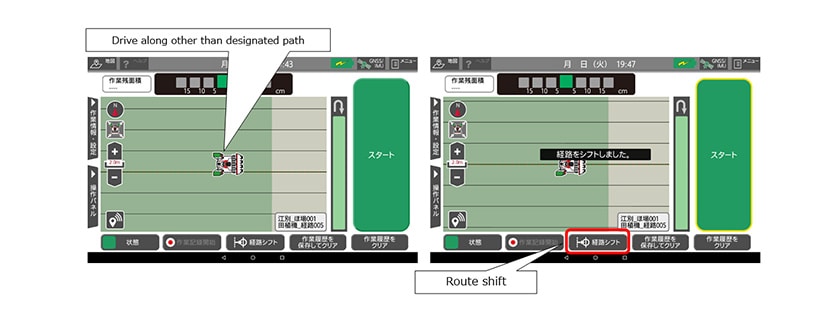
(2) Auto Mode
In Auto Mode, the rice transplanter functions automatically without requiring any manual steering input from the operator, both when moving in a straight line and when turning (see Fig. 7).
To determine the shape of the field, the area to be planted is defined by first driving the rice transplanter around its perimeter. (Once complete, this step does not need to be repeated in following years unless the shape of the field changes.) (See Fig. 8.) After specifying the shape of the field, selecting one of the four sides and specifying the start position automatically generates the paths to follow across the area to be planted and displays all of these on the tablet. The rice transplanter is then driven to the start position and transplanting commences, after which the vehicle uses automatic steering to follow the generated paths (see Fig. 9). When the seedling "Alignment Assist" function (for automatically determining where to halt planting before a turn and where to resume afterwards) is also used, the only task for the operator to perform manually is to adjust the speed (which is controlled by a foot pedal). As for Linear Mode, the vehicle position is displayed on the tablet in real time, meaning that even inexperienced operators can plant seedlings with the skill of a pro.
As accurate row spacing can be maintained even in waterlogged fields where the marker tracks are difficult to see, this reduces operator fatigue and workload, allowing them to focus instead on how well the seedlings are being planted or on checking the distribution of fertilizer or agricultural chemicals.

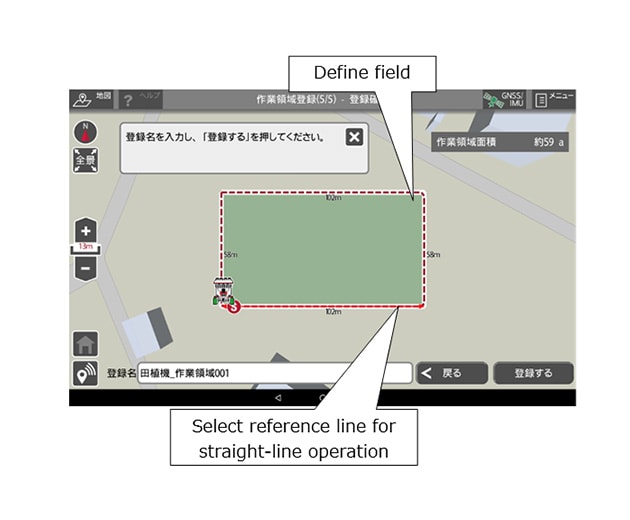
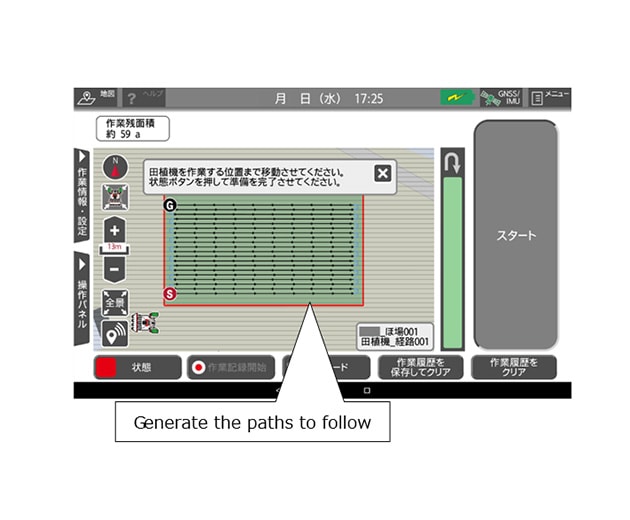
3.2. Automatic Steering System Support
The auto-rice transplanter uses its EPS as the actuator for automatic steering. The reasons for this are as follows.
- Simplifies automatic steering control (less subject to influence by external factors)
- Ensures reliable straight-line driving (good responsiveness)
- Satisfies requirement for sufficient power to turn using actuator alone
- Does not require any changes to steering or control panel layout
- Allows the re-use of most existing parts (small number of part changes)
The current YRD rice transplanter power steering mechanism uses a torque generator (to provide hydraulic steering assistance) located upstream of a steering reduction gear inside the transmission case (see Fig. 10). The EPS was fitted by replacing this unit (see Fig. 11). Using this configuration makes the most of existing parts. It also avoids any layout changes around the steering mechanism, with panel switches and the feel of manual steering remaining the same as before (see Fig. 12).
Using EPS meant that the steering assist power needed to be increased and this allowed for improvements to the feel of other manual operations (other than automatically driving in a straight line). This included reducing the level of operator effort and the incorporation of a speed-sensitive variable assist function that outputs the optimal amount of assistance based on vehicle speed and steering input torque (see Fig. 13).
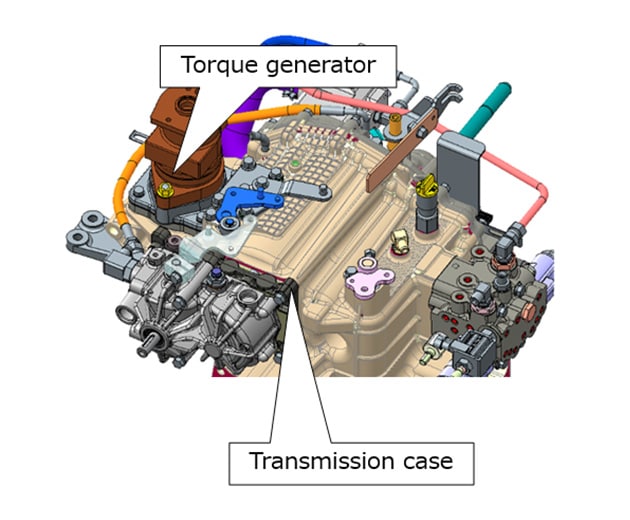
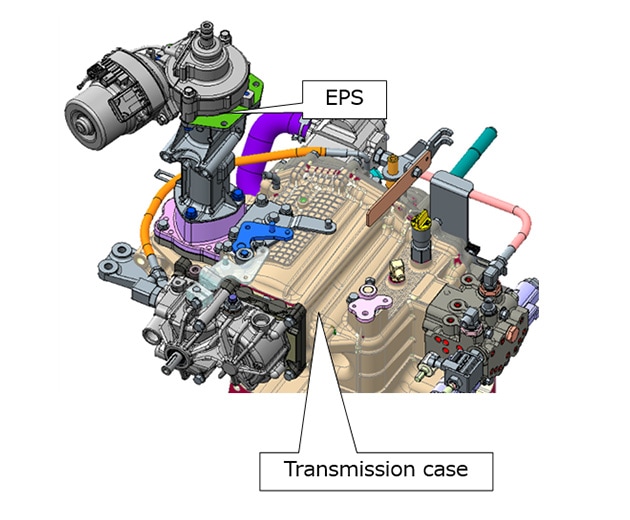
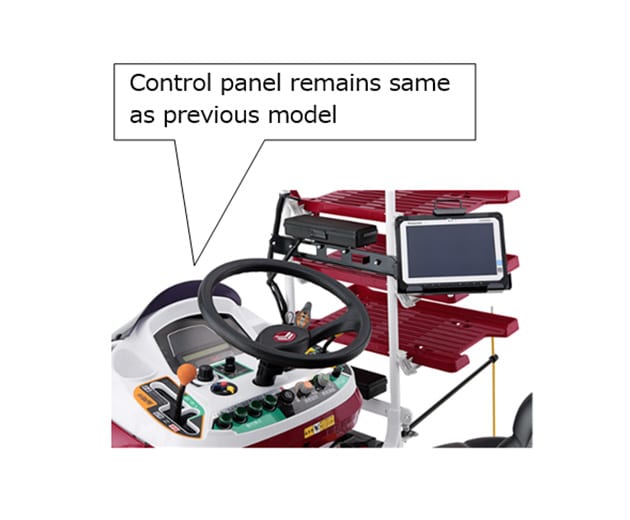
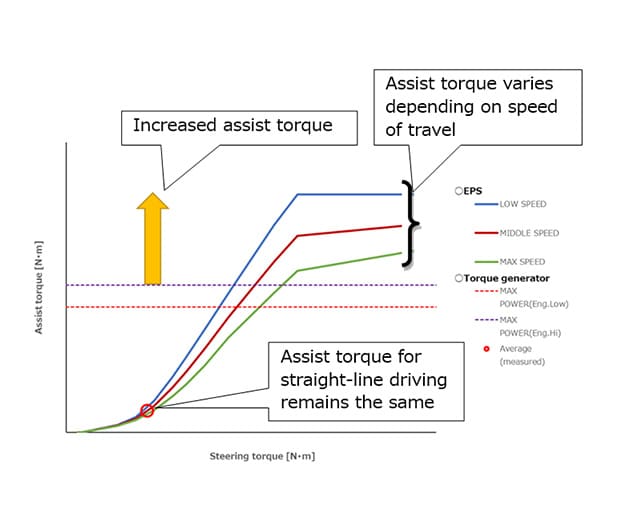
3.3. Benefits of Automatic Driving when Used with High-Density Seedlings
The greatest benefit of planting with high-density seedlings is that it reduces the number of seedling loading operations. This reduces the number of times the machine needs to stop at the side of the field to load seedlings, thereby not only reducing the workload, but also significantly shortening the time it takes to complete planting.
When the seedling "Alignment Assist" function and high-density seedlings are used together, it is possible to plant 30a without replenishing the rice transplanter with seedlings (see Fig. 14). Steering is also not required when automatic driving is used. The workload for the operator can also be further reduced and the planting time shortened by selecting Auto Mode (which includes automatic turning) to string together the rows to be planted automatically, thereby consolidating the areas in the field that can be planted at one time (see Fig. 15).
Spring-time work (plowing, leveling, raising seedlings, and transplanting) makes up about 40% of wet rice cultivation, and farmers want to be able to work efficiently during busy periods when a lot of work needs to be done at the same time. Using high-density seedlings and automatic driving offers a solution that can boost capacity and reduce fatigue.
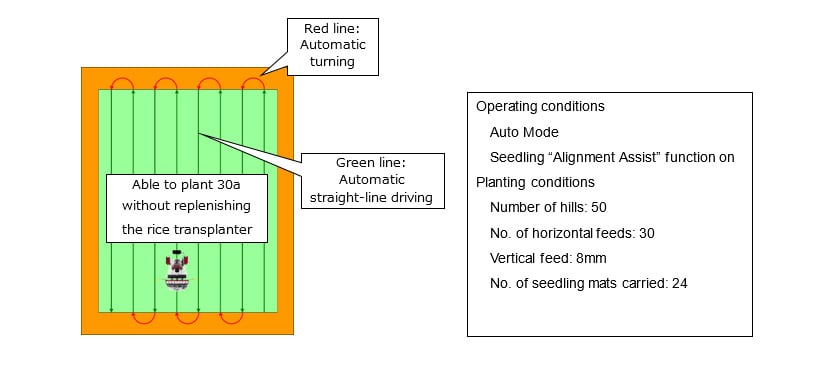
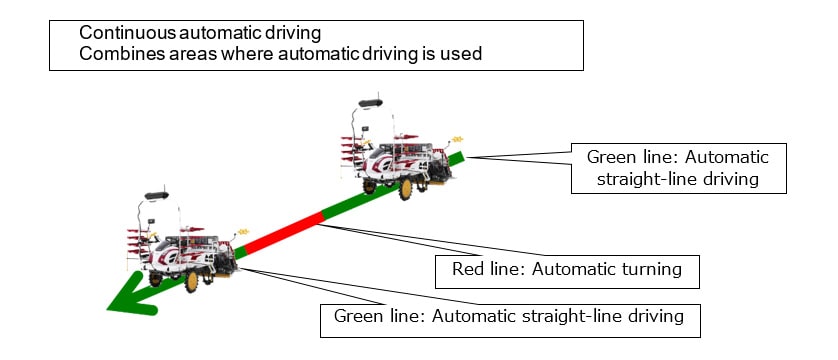
4. Conclusions
Having already achieved labor savings through its high-density seedling technology, Yanmar has gone on to develop a rice transplanter that incorporates automatic driving technology created for the Robot Tractor to provide even greater labor savings and efficiency. Yanmar anticipates that these two technologies will become standard features on rice transplanters in the future.
The automatic driving is based on the use of satellite positioning information, with correction information also currently available by a variety of means, an area in which the infrastructure is still being put in place. As better infrastructure becomes available in the future, with further advances and consolidation, there will be a need to observe closely which method becomes adopted for mainstream use for this purpose.
Yanmar also anticipates growing diversity in what customers want from automatic driving (whether they prioritize precision and efficiency or cost), and aims to further raise customer satisfaction by delivering solutions that suit these different needs.
-IMPORTANT-
The original technical report is written in Japanese.
This document was translated by Research & Development Management Division.
Author
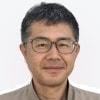