Research & Development Center
YANMAR Technical Review
Application of Low-Viscosity Oil to Diesel Engine Valve Train
Abstract
Significant improvements of fuel economy have been urgent in the industry under the global warming issue. Modifications of power source for higher fuel efficiency have been big trend nowadays, and lower viscosity lubricating oils for internal combustion engines have been very common in the market. Though lower viscosity lubricating oil could improve fuel efficiency, they may also lead to excessive wear of sliding surfaces such as slider bearings. We proposed a wear analysis model for sliding surfaces under mixed lubrication and applied it to rocker arms of valve train of small sized diesel engines. It was verified that the optimized design of the rocker arm can meet wear criteria with engine durability tests using a low viscosity lubricating oil.
1. Introduction
With reducing emissions of greenhouse gases posing a challenge for industry as a whole, there is rising demand for energy efficiency in industrial machinery, including the introduction in Japan of fuel efficiency standards certification for construction machinery. There is also strong demand for lower fuel consumption in the diesel engines that power these machines, with low-viscosity lubricating oils coming on the market that claim to improve fuel efficiency. Unfortunately, reducing the viscosity of lubricating oil results in thinner oil film thicknesses and increases the risk of reliability issues such as seizing or wear, requiring changes such as to engine designs or to the composition of additives.
The research described in this article looked at engine valve train components that are at risk of increased wear when using lower viscosity oil, and used a wear analysis model to study suitable engine design improvements. Wear evaluation tests were conducted to assess these improvements, finding that the wear on the inner surface of the rocker arm hole was equal or less than that using oil of standard viscosity.
2. Test Method
2.1. Fuel Consumption Evaluation
Table 1 lists the specifications of the industrial diesel engine used to evaluate the fuel consumption. Lubricating oils with the same additive formulation as the genuine oil for the engine, but with kinematic viscosities of 100 °C adjusted to SAE30, SAE20, and SAE8 viscosity grade by using different base oils.
Table 1 Specifications of Applied Engine
Number of cylinders | Cylinder bore, mm |
Stroke, mm |
Rated speed, min-1 |
Rated output, kW |
---|---|---|---|---|
4 | φ88 | 90 | 3000 | 35.5 |
2.2. Wear Evaluation
Fig. 1 shows the experimental apparatus used to evaluate the wear. To focus on the evaluation of valve train wear, the engine was driven by an external motor through the crank shaft. The lubricating oils described above were supplied by an external device at a temperature and pressure of the actual engine.
For the operating mode, a wear evaluation pattern for an industrial engine alternating between rated speed and idling was adopted. The wear was calculated by measuring the component dimensions by a micrometer before and after 250 hours of the wear evaluation test.

3. Test Results
3.1. Fuel Consumption
Fig. 2 shows the fuel consumption at rated power. This shows that fuel consumption has a linear correlation with kinematic viscosity of 100 °C, with the results for SAE8 oil being approximately 6 g/kWh better than for SAE30 oil.
3.2. Wear
Fig. 3 shows the relative wear (a ratio to the wear using SAE30 oil) of the rocker arm hole, as an example of the results of wear evaluation test. The wear increases as lubricating oil viscosity decreases, with the wear using SAE20 oil being above the wear limit. The wear analysis model was then used to study engine design improvements to verify their effects.
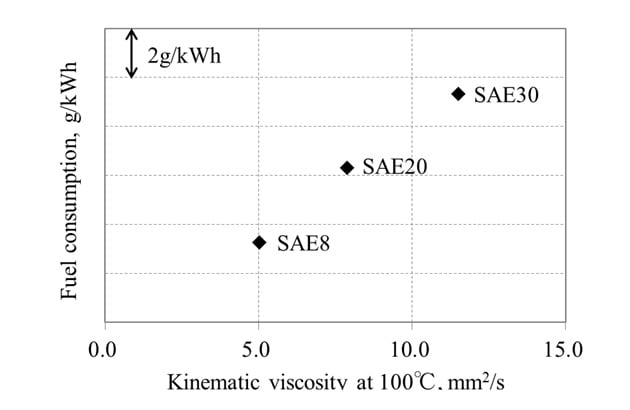

4. Study of Wear Improvements
4.1. Verification of Wear Analysis Model
Before studying wear improvements, the practicality of the wear analysis model was first verified. Wear is obtained by calculating the instantaneous wear rate during the motion of the rocker arm and then integrating over this time. The Holm equation (1) and the Greenwood & Tripp equation1) (2) are used to obtain the wear rate (


Fig. 4 shows the calculation results and experimental measurement results as a solid line and circles respectively with the relative wear. The results are expressed with the kinematic viscosity of 100 °C, which is the actual engine oil temperature, as a horizontal axis. The graph shows good agreement between the calculated and measured results.
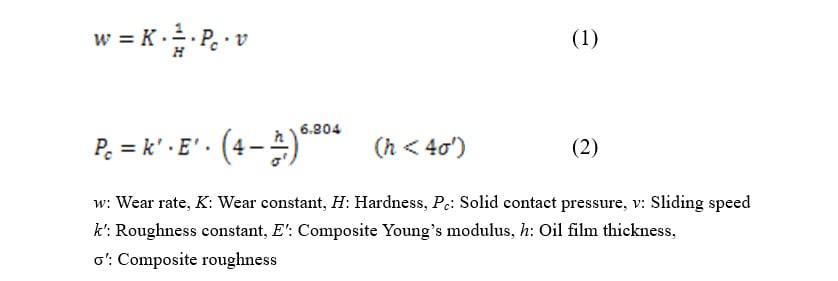

4.2. Study of Improvements
The wear analysis model was then used to study possible improvements. However, because design constraints prevented changes to any of the main dimensions, changes to material hardness were considered instead.
Fig. 5 shows the relationship between relative wear and the hardness of the inner surface of the rocker arm hole. As indicated by equation (1), hardness and wear are inversely proportional. From this it was determined that a hardness of 450HV would be needed to satisfy the wear limit shown in Fig. 3. An appropriate surface treatment was chosen and applied to a prototype.
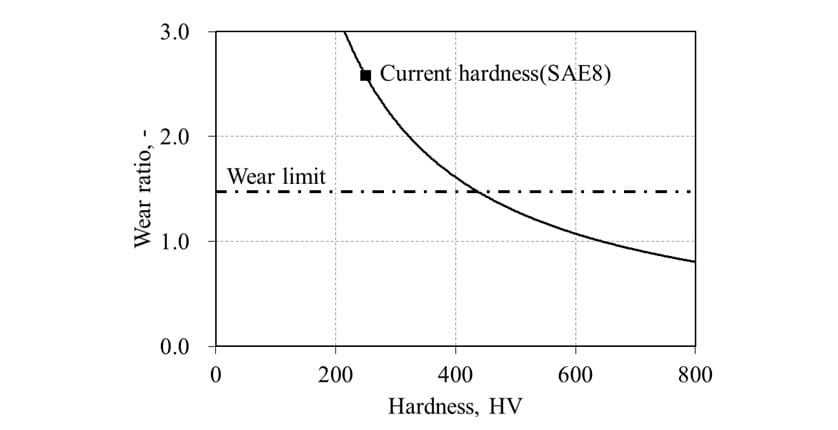
5. Verification of Wear Improvement and Additional Remarks
The effect of surface hardness was verified with the wear evaluation test. Fig. 6 shows the wear of the prototype rocker arm by SAE8*. It shows that the wear of the prototype rocker arm with the surface treatment is far less than the wear limit. Possible reasons for the divergence between the predictions of the wear analysis model and wear evaluation test results include changes to surface roughness due to initial conformability or changes over time in the macro-contours. Accordingly, there is a need to develop a wear prediction method that considers these effects in order to improve future accuracy.

6. Conclusions
This research reveals the following.
- Fuel consumption at rated power using SAE8 viscosity grade lubricating oil is approximately 6 g/kWh less than when using SAE30 oil.
- The results of wear evaluation test indicate that reducing lubricating oil viscosity increases the wear of the inner surface of the rocker arm hole.
- It was demonstrated that the wear analysis model can provide a quantitative indication of the change in wear due to lubricating oil viscosity.
- As a result of using the wear analysis model to study design improvements for the rocker arm hole, it was demonstrated that the wear was improved by more than predicted.
- Improvements to wear prediction accuracy will require a wear prediction method that considers changes over time in surface roughness and macro-contours.
Finally, the author would like to take this opportunity to express his thanks to the Central Technical Research Laboratory of JXTG Nippon Oil & Energy Corporation, who provided the oil used for testing.
Reference
- 1)Greenwood J.A. and Tripp J.H.: The Contact of Two Nominally Flat Rough Surfaces. Proceeding of the Institution of Mechanical Engineers, Vol.185,48,1970,pp.625-633.
- ◊This article is a reprint of one that appeared in the Proceedings of the 2017 Fall Tribology Conference in Takamatsu (presentation A1) published by the Japanese Society of Tribologists.
-IMPORTANT-
The original technical report is written in Japanese.
This document was translated by Research & Development Management Division.
Author
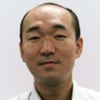