Development Division
Development Planning Division
YANMAR AGRIBUSINESS CO., LTD.
YANMAR Technical Review
Self-Driving Robot Tractor: Yanmar Technology for Sustainable Agriculture
Abstract
Yanmar "Robot Tractor" can drive and work in the farmland along a predetermined path accurately and safely by using the positioning technology, which determines the current location and corrects positioning error, and safety technology, which detects and shows obstacles in blind-spots under visual observation. A tablet user interface that provides intuitive operation makes control of the tractor easy.
This article describes functions and technologies incorporated in "Robot Tractor", the first product in its "Smart Pilot" series of self-guided agricultural machines. ("Smart Pilot" is the brand name for product lines that incorporate Yanmar's self-driving technology).
1. Introduction
Agriculture is facing a difficult environment with a population of farmers that is both ageing and shrinking, a trend that will only accelerate further in the future. Based on its brand statement of “A SUSTAINABLE FUTURE: Providing sustainable prosperity through technology”, Yanmar's aim is to transform agriculture into "agro-industry" in order to achieve sustainability. As part of this, the company has engaged in the research and development of techniques for the precise self-guiding of vehicles, intuitive operation, and safety assurance, drawing on technologies from across the Yanmar Group and culminating in the launch of the "Robot Tractor", the first in its "Smart Pilot" series of self-guided agricultural machines.
2. Product Profile
The Yanmar robot tractor (see Fig. 1) has a tablet user interface and is fitted with a global navigation satellite system (GNSS) unit specially developed by Yanmar that allows the tractor to drive itself over farmland along a predetermined path. The system enables a single driver to operate two tractors in coordination (a robot tractor and the operator-driven tractor) (see Fig. 2). The robot tractor is also fitted with safety devices in accordance with the safety guidelines for self-guided agricultural machinery issued by Japan's Ministry of Agriculture, Forestry and Fisheries, which means the system is also able to operate the tractor on its own under human supervision. Along with its robot tractor functions, the tractor is also equipped with automatic tractor functions (automated operation with an operator in the driving seat) and automatic steering so that it can be used in ways that suit different customer requirements.
Yanmar's Smart Assist is a system for collecting machine and other information at a Yanmar data server to provide useful farm management information for analysis and other uses. It uses information and communication technology (ICT) to enable records of robot tractor operation to be managed centrally.


3. Features
3.1. Precise Automatic Driving Control
(1) Development of RTK-GNSS (Real Time Kinematic - Global Navigation Satellite System) integrated unit
Yanmar's proprietary GNSS unit (see Fig. 3) determining the robot tractor's current location and an inertial measurement unit (IMU) installed in the robot tractor correcting the positioning error, make precise positioning control to ensure accurate agricultural works. Yanmar has also developed its own small and portable base station unit (see Fig. 4) to enable use of the robot tractor at locations where no base stations have been installed by the local government or agricultural cooperatives (JA).


(2) Automatic driving control
An algorithm to control an automatic driving of the tractor based on various settings and information from RTK-GNSS unit and sensors was developed. By preventing positioning errors caused by the contours of the farmland and other conditions experienced by the tractor during operation, precise straight-line driving performances without erratic weaving are achieved. For control of turning, turning areas are determined apart from the straight-line driving area and different tractor speed and engine speed in each area can be used. A turning control algorithm was developed for turning the tractor based on turning radius and other predefined settings, providing a smooth transition of control from straight-line to turning so that the tractor can enter its new straight-line trajectory correctly without weaving.
3.2. Simple and Intuitive Operation
The robot tractor is fitted with a tablet user interface that provides intuitive operation and makes control of the tractor easy. In addition to using a map installed in the tablet to provide a visual representation of the location of the robot tractor and the farmland being worked, the tablet user interface is also used for registration of land information (see Fig. 5), implements settings (see Fig. 6), the area within the farmland that is to be worked (see Fig. 7), and the path to follow (see Fig. 8). These registrations are then used to automatically select a path over the farmland that is optimal in terms of its contours before starting automatic driving (see Fig. 9). This makes the robot tractor easier to use because it means users do not have to specify path and other appropriate settings for themselves. The farm and other entered data are managed centrally by Smart Assist, along with position information, and is available for viewing in the form of work records.

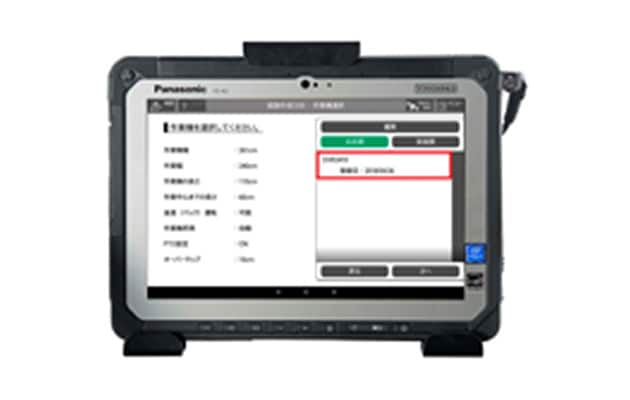

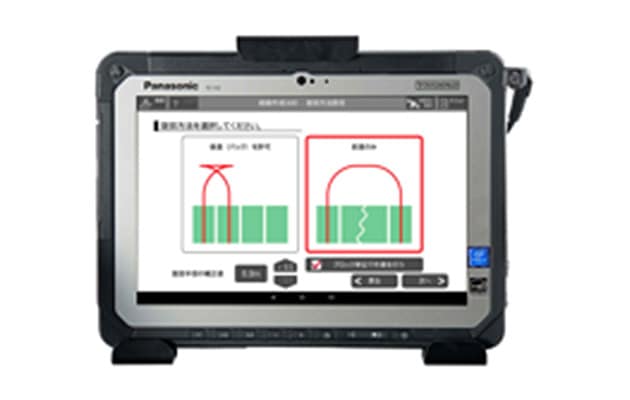
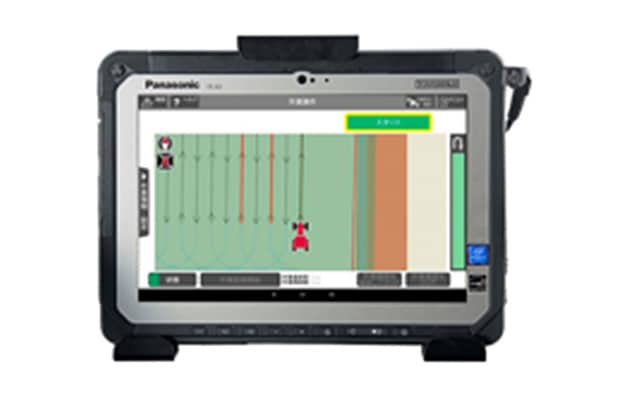
3.3. Development of Safety Assurance Techniques
To ensure safety, the system was developed in compliance with the safety guidelines for self-guided agricultural machinery issued by Japan's Ministry of Agriculture, Forestry and Fisheries on March 31, 2017 (see the ministry website for more information).
(1) Safety functions
The tablet user interface is used to start and stop the robot tractor (see Fig. 10). Predefined robot tractor settings such as vehicle speed and engine speed can also be adjusted during operation based on the land conditions. The robot tractor is also fitted with an I-HMT continuously variable transmission that enables smooth driving together with safe and efficient operation.
As a safety backup, the tractor also comes with an emergency stop remote control to provide an alternative means of stopping the vehicle without using the tablet user interface.
The robot tractor is also equipped with a control algorithm that can shut down all functions safely. This is invoked if the robot tractor is about to leave the registered farmland area, if it diverges by more than a certain amount from its target path in a straight-line or turning areas, or if communication functions are interrupted.

(2) Safety devices
The robot tractor is fitted with cockpit cameras that show the view in front of and behind the robot tractor on the tablet user interface (see Fig. 10), providing coverage of surveillance blind-spots. The safety systems also include a laser sensor and ultrasonic sensor for detecting obstacles around the tractor (see Fig. 11). A commercially available laser sensor was combined with an algorithm developed specifically for agricultural machinery to ensure that the tractor could operate safely in the sort of conditions it would encounter in practice without stopping unnecessarily. Rather than stopping immediately on detection of an obstacle, a deceleration algorithm is provided that, under certain conditions, instead controls vehicle speed on a time-to-collision (TTC) basis.

3.4. Modular Design Provides Variety of Options
Along with the specifications of the tractor itself, the Yanmar robot tractor is also available as an option on existing models (to inquire about which models support this option, visit: https://www.yanmar.com/jp/support/contact/). To facilitate the introduction of the robot tractor and build familiarity with use of automatic driving, Yanmar has implemented the features required for automatic driving as separate units and modules. By doing so, Yanmar has made it possible not only to provide both automatic tractor and robot tractor functions and the upgrading from one to the other, but also to offer these as options on existing models to enable use of tractors already in the marketplace. This enhances lifecycle value (an indicator of how much value is added by a particular agricultural machine during the course of its life) and makes it easier for customers to start using robot tractors.
3.5. Benefits of Using Robot and Operator-Driven Tractors
To overcome the challenges facing agriculture (including a shrinking and aging workforce), to achieve dramatic labor savings and large-scale production, and to make agricultural work something that anyone can participate in, Yanmar has set out to enable robots and people to perform agricultural work in coordination that are accessible to everyone, accurate, and efficient.
The benefits of robot and operator-driven tractors coordinated operation include a significant increase in work efficiency (see Fig. 12).

In the first use case, a robot tractor and operator-driven tractor perform the same tasks simultaneously, meaning that the operator gets through twice as much work as they would otherwise. Furthermore, even if the operator does not have much experience, he/she can work accurately in a straight line by following the path of the robot tractor and only working on areas where the robot tractor does not work (case 1 in Fig. 12).
In the second use case, a single operator can perform two different tasks at the same time. One example would be for the robot tractor to first till the ground while the operator-driven tractor follows along behind sowing seeds. This increases work efficiency by performing multiple tasks at once (case 2 in Fig. 12). Doing so also significantly shortens the time taken for the work, reducing weather dependence and helping the work proceed on schedule.
4. Conclusions
Development of the robot tractor was born out of a desire to address farming issues and the challenges facing customers, with Yanmar launching a project to commercialize the technology that involved various different divisions working together on the development. The concept behind the development was to provide: (1) Precise automatic driving control, (2) Intuitive operation, and (3) Safety assurance technologies, and to allow for the retrofitting of existing tractors already in the marketplace rather than only offering the feature on a particular model of tractor.
As sales of the robot tractor begin in earnest, Yanmar intends to further develop it into an effective system based on customer feedback and requests. Yanmar technologies developed for the robot tractor will also be deployed on tractors and other agricultural machinery developed by the company to create an agricultural workplace in which use of self-guided machinery is routine and available to anyone.
-IMPORTANT-
The original technical report is written in Japanese.
This document was translated by Research & Development Management Division.
Author
