Development Dept.
KANZAKI KOKYUKOKI MFG. CO., LTD.
YANMAR Technical Review
Low-Noise Technology for Gear Design
Abstract
This article describes the simulation technology concerning silencing of power transmission gears. Generally, gear noise is unpleasant because of high frequency noise which is generated by the rotational fluctuation (transmission error) which is caused by the tooth flank shape and manufacturing error. In order to reduce the transmission error, it is necessary to determine an appropriate tooth profile in consideration of the influence of multiple factors.
The simulation technology for transmission has been using in product design since 2012. An example that transmission error and gear noise are reduced by optimizing tooth profile using this simulation technology is shown.
1. Introduction
As a component manufacturer within the Yanmar Group, Kanzaki Kokyukoki Mfg. Co., Ltd. develops, manufactures and sells hydraulic equipment and various transmissions. The company possesses considerable experience and know-how in areas ranging from design through to manufacturing technology, particularly with respect to the gears that serve as key components in transmission systems. Meanwhile, the trend toward faster vehicle speeds and greater comfort in recent years is driving a strong demand for reducing gear noise, something that is difficult to achieve using conventional technology. This article describes the simulation technology for reducing gear noise that Kanzaki Kokyukoki Mfg. is currently working on.
2. Types of Gear Noise
Gear noises in transmissions are generally classified as either whine noise or rattle noise (see Table 1). A high whine noise is a high frequency noise and is mainly caused by small errors in the gear tooth profile and tooth stiffness. A rattle noise, in contrast is the impact noise of contacting gear tooth flank and is mainly caused by the fluctuating input load to the gear or clearances between the teeth flanks (backlashes). As it is often the case that gear whine is the main problem in the products handled by Kanzaki Kokyukoki Mfg., the company focuses on determining the suitable tooth profile at the development and design stage and on quality checks for machined gears.
Table 1 Types of Gear Noise and their Characteristics

3. Mechanism of Whine Noise Generation
Gear whine occurs when vibrations driven by small fluctuations in rotation caused by the tooth profile or manufacturing error are transmitted via the bearings that support the gear shaft to the housing, resulting in vibration on the surface of the housing (see Fig. 1).
These fluctuations in rotation are due to errors in the rotational angle of the gear teeth as they meshes, what is known as transmission error.

The causes of transmission error can be further classified into geometrical factors and factors due to tooth stiffness. In the case of geometrical factors (see Fig. 2), a deviation from the ideal involute mesh occurs due to assembly error or deflection of the shaft, and this results in the rotational angle of the driven gear being retarded or advanced. Moreover, fluctuation of the rotational angle occurs if the tooth flank is uneven.

In the case of factors due to tooth stiffness (see Fig. 3), the mesh stiffness varies depending on how many teeth are in contact at any given time, and this results in fluctuation of the rotational angle of the driven gear.
In other words, the geometrical factors and factors due to tooth stiffness act in complex manner to vary the transmission error, thereby producing the exciting force. This means that, in designing an appropriate gear that has low noise, these factors need to be considered when deciding on the tooth profile.

4. How to Reduce Transmission Error
As noted above, a number of factors must be considered in order to reduce transmission error in gears.
Fig. 4 shows the relationships between torque and transmission error for a helical gear with an ideal involute profile (unmodified) and another for which the tooth profile has been modified arbitrarily. Here, tooth profile modification means that an error from the ideal involute profile is intentionally provided to the tooth profile, as shown on the right in Fig. 4. The unmodified gear with less profile error provides better performance with regard to transmission error fluctuation when the load torque is low whereas the gear with a modified profile is better above a certain level of load torque. This shows how fluctuations in transmission error can be minimized by modifying the tooth profile to suit the load applied to the gear.
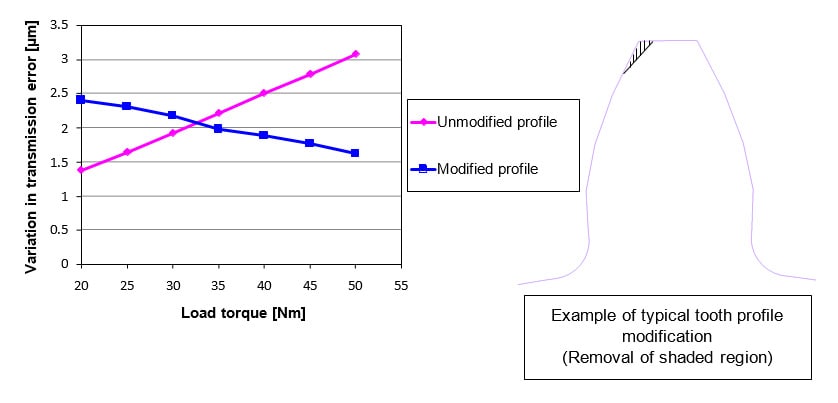
To predict the various influences to which a gear will be subject in a transmission system and to take these into account at the design stage, Kanzaki Kokyukoki Mfg. has established the simulation technology that it has been using in product design since 2012 (see Fig. 5). Using details of tooth profiles for different types of gear as input, the technology can evaluate parameters like transmission error and strength under actual operating conditions by considering the deformation of the gear shaft and bearings.

5. Example Application to Product Design
The example described below involves reducing gear transmission error in a reduction gear for a utility vehicle .
In this case, the aim is to reduce transmission error by investigating how to modify the three-dimensional tooth profile of a bevel gear during the initial design stage, taking account of the tooth profile deviation resulting from deformation of the shaft, bearings, and other components as shown in Fig. 6.

To confirm the performance benefits of the improved tooth profile, measurements of the tooth profiles, transmission errors, and meshing noise were performed for the improved gear and a current production gear.
The results for transmission error are shown in Fig. 7, with the measurements on the left and an order tracking analysis results of these measurements on the right. The comparative meshing order results demonstrate that the improved gear has less variation in transmission error.
The measurement results for meshing noise shown in Fig. 8 demonstrate a significant reduction in noise at the second- and third-order meshing frequencies of the improved gear.


6. Conclusions
This article has described the simulation technology established by Kanzaki Kokyukoki Mfg. for reducing gear noise. The technology is being utilized in new development projects where it helps with performance prediction at the design stage. In the future, it is expected that this simulation technology continue supplying solutions to delight customers by reducing the size and increasing the output power of products with high reliability.
-IMPORTANT-
The original technical report is written in Japanese.
This document was translated by Research & Development Management Division.
Author
