Engineering & Development Dept.
YANMAR CONSTRUCTION EQUIPMENT CO., LTD
YANMAR Technical Review
Technologies used in New C30R-3 Crawler Carrier: Ease-of-Operation and Capacity for Work Enhanced by Adoption of 2P2M System
Abstract
A crawler carrier is a construction machine with crawler tracks and a dump vessel for carrying loads. It is used to carry sand or other construction materials to sites that are difficult to access by a dump truck or conventional truck due to rough ground condition. The C30R described in this article has long been a top seller in the YCE (Yanmar Construction Equipment Co., Ltd.) product range with 60% of the Japanese market.
The complete new model incorporates many improvement requests and makes the machine easy for customers to use while still retaining the durability and driving performance that have been so well regarded on previous models.
This article describes the new carrier and the features and technologies of its new hydraulic system that has been significantly upgraded compared to the previous model in order to satisfy the design concept.
1. Introduction
A crawler carrier is a type of construction machine with crawler tracks and equipped with a dump vessel for carrying loads. This type of machine is categorized under Japanese law as a vehicle for use on uneven ground, and is widely used to carry sand or other construction materials to sites that are inaccessible by a dump truck or conventional truck due to soft or uneven ground condition. Small crawler carriers in particular are widely used in mountainous locations with narrow driving access or for tasks such as river remediation work.
Recognized for its durability and driving performance ever since the first model went on sale in 1991, the C30R described in this article is a small crawler carrier that for many years has been the market leader in Japan with a share of more than 60%.
For 2017, Yanmar is launching a completely new C30R to coincide with changes in exhaust gas emission regulations in Japan and overseas. The new generation of C30R is an innovative new machine that is at the forefront of the market, having addressed a wide variety of improvement requests while still retaining the durability and driving performance that have been so well regarded on previous models. This includes the formulation and commercialization of a development concept aimed at making the C30R suitable for overseas markets and enhancing its ease-of-operation, a subject of many of the improvement requests.
This article provides an overview of the new C30R-3 and describes the features and technologies of its new hydraulic system that has been significantly upgraded compared to the previous model in order to satisfy the development concept.
2. Product Overview
The new C30R-3 (shown in Fig. 1) combines environmental performance and enhanced capacity thanks to its new hydraulic system and a high-output, electronically controlled, common rail engine with a Yanmar diesel particulate filter (DPF) that complies with the 2014 Japanese emission regulations for "non-road special motor vehicles". Moreover, a new version with a rotating vessel has been added to meet the requirements of overseas markets, this specification accounting for 80% of demand in Europe.


Fig. 1 New C30R-3 Crawler Carrier
3. Features of the C30R-3
In place of the single-pump/single-motor + transmission system used on the previous model, major changes have been made to the traveling hydraulics, making the C30R-3 the first small crawler carrier on the Japanese market to adopt a dual-pump/dual-motor system that is controlled by a single lever (see Fig. 2). The features of this new hydraulic system are described below in terms of ease-of-operation, comfort, and economics.

3.1. Ease-of-Operation
Using a system with a dual-pump/dual-motor has significantly improved steering freedom because the right and left crawlers can now be controlled independently, allowing spin turns and gentle turns that were not possible on the previous model. By reducing the minimum turning radius, the ability to perform spin turns further improves the machine's performance in confined spaces (see Fig. 3).
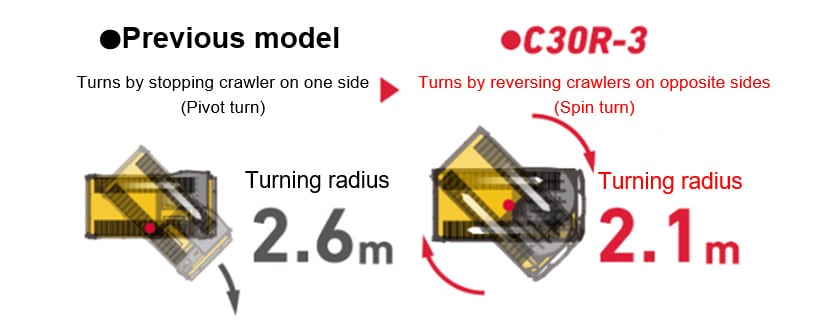
Moreover, whereas the previous model was subjected to significant ongoing shocks due to its being steered using a brake to forcibly stop the crawler on one side in an on/off manner, the new model features smooth steering because it is steered by controlling the flow from the right and left travel motors.
3.2. Comfort
The C30R-3 is the first small crawler carrier in the Japanese market to offer single-lever control, with a single wrist control lever that can be used to control forward motion and perform pivot turns, spin turns, and gentle turns (see Fig. 4). Intuitive and comfortable driving operation is provided by inputting a proportional control signal to the pump based on the angle of the wrist control lever. This means that the crawler carrier moves in the direction in which the lever is tilted and accelerates or decelerates in accordance with the lever angles tilted.

3.3. Economics
To reduce fuel consumption compared to the previous model, an "eco mode" is provided together with a control function that utilizes an automatic speed selection mechanism that switches the travel motors to a low speed when under high load to automatically select the optimal speed that eliminates hydraulic losses. This reduced fuel consumption by 13% compared to the previous model when measured using a Yanmar test pattern.
Eliminating the transmission also reduces running costs because it is no longer necessary to perform a friction plate replacement every 300 hours.
4. Technologies Used
This section describes the technologies adopted in response to the new challenges that emerged as a result of changing to a dual-pump/dual-motor system to improve operational performance.
4.1. Achieving Torque Matching without Compromising Capacity for Work
Because the use of a dual-pump/dual-motor system means that the hydraulic torque when driving one side is only half that when driving both sides, the hydraulic torque needs to be much greater than on the previous model if it is to achieve the same capacity for work. Whereas increasing the engine size to provide this additional hydraulic torque would result in higher costs and higher fuel consumption, seeking to maintain the same capacity for work using a similar engine size to the previous model risks the engine stalling under high load (see Fig. 5).
To prevent engine stalls while still maintaining the capacity for work using a similar engine size to the previous model, A hydraulic pump speed sensing control was adopted to reduces the pump discharge rate according to the decrease of the engine speed (see Fig. 6).


The use of hydraulic pump speed sensing control allows the optimal torque to be specified and improved the capacity for work by 30% compared to the previous model when measured using a Yanmar test pattern. This succeeded in preventing engine stalling without compromising the machine's capacity for work. Hydraulic pump speed sensing control also helps keep costs down because it does not need to be electronically controlled and therefore does not require a controller.
4.2. Ensuring Parking Performance on Sloping Ground
Because they are often used in mountainous terrain, small crawler carriers must be able to park on sloping ground. With the use of a dual-pump/dual-motor system having doubled the number of pumps and motors, the amount of leakage from the hydraulic system is higher and this also increases the rate at which the machine moves downhill under its own mass when parked on a slope.
To ensure parking performance on sloping ground, shift-down control was adopted to automatically switch to the volume for low-speed of the travel motors when the machine is stopped (see Fig. 7).

When measured using a Yanmar test pattern, shift-down control reduced the speed at which the machine moved downhill under its own mass by 30% compared to the previous model. Also, because it starts at the low-speed shift, the machine always start to travel smoothly when starting even if the control lever is moved quickly.
5. Conclusions
To achieve the ambitious goal of both addressing requests for improvements that remained from the previous model and making it suitable for overseas markets, Yanmar embarked on product development for the new C30R-3 by significantly upgrading its systems compared to its predecessor. The development of the dual-pump/dual-motor system controlled by a single lever, the first time such a challenge had been tried on a YCE, uncovered a number of difficulties that had not been anticipated at the planning stage. Having undergone a product development process in which each of these difficulties was overcome, one after another, Yanmar is confident that the new C30R-3 will provide greater value to large number of customers.
Yanmar intends to continue developing products that satisfy its customers by gathering feedback and taking a customer's eye view to its plans for further developments.
-IMPORTANT-
The original technical report is written in Japanese.
This document was translated by Research & Development Management Division.
Author
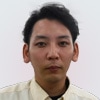