Development Division
Large Power Products Management Division
Power Solution Business
YANMAR Technical Review
6/8EY33 Series of High-Power and Fuel-Efficient Diesel Engines~Raising Life Cycle Value for the Customer~
Abstract
The development concepts behind the EY series are "raising life cycle value for the customer" and "harmony with the global environment". The EY33 draws on Yanmar’s accumulated development experience and the latest simulation techniques to provide the highest power and best fuel economy of any engine in the EY series. The new engine also improves life cycle value for the customer, with better component durability that has made it possible to lengthen maintenance intervals by 1.5 times compared to the previous model. As an environmentally friendly engine, the EY33 is contributing to the achievement of a sustainable society through its compliance with the latest exhaust gas emission regulations.
1.Introduction
Yanmar has developed its EY series of large marine diesel engines that feature low fuel consumption and excellent durability based on the concepts of "raising life cycle value for the customer" and "harmony with the global environment".
The new EY33 engines are the flagship models of the series and have the highest power of any Yanmar diesel engine. The culmination of all of the technologies built up through past development of the EY series, EY33 engines comply with the latest environmental regulations and were developed to be kind to the earth, including being designed for lower nitrogen oxides (NOX) and carbon dioxide (CO2) emissions as well as high levels of fuel economy and durability (see Fig. 1 and Table 1).
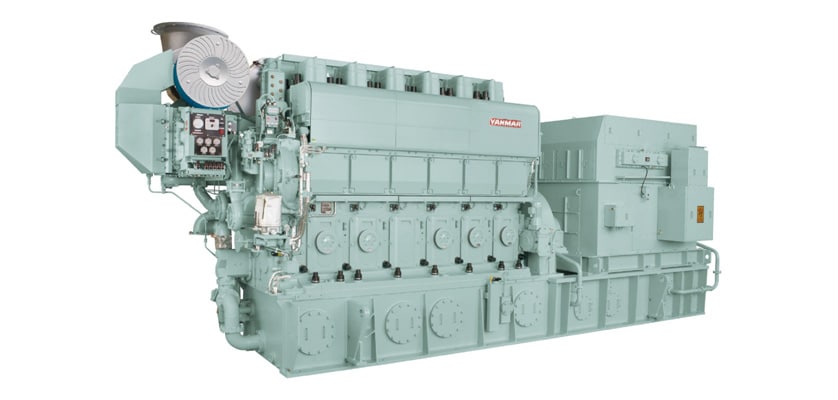
Table 1 Auxiliary Marine Engine Specifications

2.Product Technologies
2.1.High Output and Compact Design
Despite being roughly the same size, EY33 engines have approximately 18% higher mean effective pressure and 30% or higher output power than the previous N330 engines with the same bore, and have the highest level of power per cylinder of any medium-speed engine in their class.
This increased power means that a six-cylinder EY33 engine can deliver a similar level of power to previous eight-cylinder engines, significantly reducing its mass and the space required for installation (see Fig. 2 and 3).
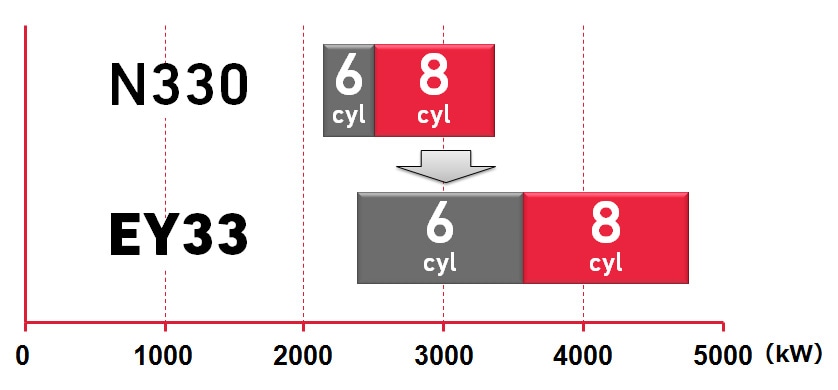

2.2.Low Fuel Consumption
To overcome the challenge of achieving both low NOX emissions and low fuel consumption, the EY series engine use a high-pressure Miller cycle system that combines a Miller cycle cam and a turbocharger with high pressure ratio (see Fig. 4).
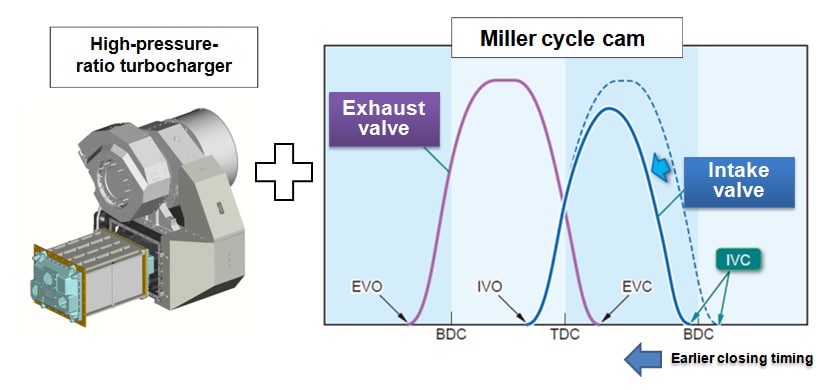
The high-pressure Miller cycle system is a way to reduce fuel consumption when complying with NOX regulations by reducing the intake air temperature at the end of the compression stroke to minimize NOX generation through the use of a Miller cycle cam that closes the intake valve at an early timing, and a high-pressure-ratio turbocharger that is able to supply the cylinder with the amount of air needed for good combustion during this shorter intake period.
To determine the combustion parameters for the EY33, an optimal set of parameters that minimized the emission of NOX and soot was obtained using a 3D combustion simulation, the accuracy of which was improved by feedback from combustion observation on an actual engine (see Fig.5) as well as test data acquired during the development of other engines in the EY series. This improved fuel consumption by more than 5% compared to the previous engine (see Fig. 6).
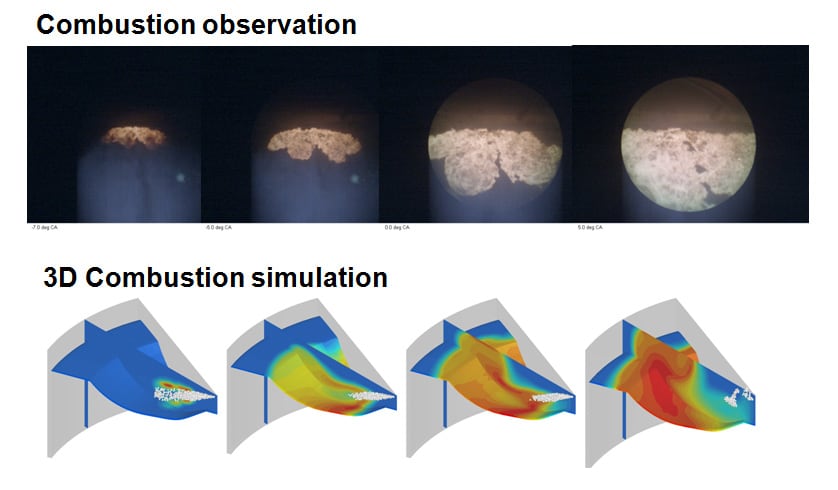

2.3.Improvements to Durability and Reliability
To achieve a higher level of long-term reliability and greater durability as well as increasing power, advanced numerical analyses based on 3D design data were used in the development of the engine to optimize component design specifications (see Fig. 7).

The maintenance intervals of key components were lengthened to 1.5 times those of the previous model by extending component life time through the use of techniques for preventing the buildup of deposits in the combustion chamber and techniques that are resistant to contamination so as to maintain long-term reliability even when running with H.F.O. (heavy fuel oil) (see Table 2).
Together with better fuel economy, improvements to component durability help improve life cycle value (LCV) for customers by reducing the increase in lubricant consumption that occurs over time due to wear.
Table 2 Techniques for Preventing Buildup of Deposits in Combustion Chamber and Resisting Contamination

2.4.Harmony with Global Environment
By matching the engine with a Yanmar selective catalytic reduction (SCR) system, reliability has been achieved in long-term use under the latest Tier 3 NOX regulations of the International Maritime Organization (IMO). Similarly, for the use of low-sulfur fuels, which tend to be less viscous, in order to comply with marine regulations for sulfur oxides (SOX), which are also being tightened, the Yanmar PF fuel injection pump is adopted. It has a structure that a plunger and its driving parts are separated and as any fuel leaking from the clearance between plunger and barrel does not mix with the lubricant, reliability has been achieved. Also, to reduce use of environmentally hazardous substances, a lead-free aluminum alloy is adopted for the crank pin and journal bearings that require periodic replacement, and a digital exhaust thermometer is used in place of mercury contained one.
3.Conclusions
The first EY33 was shipped in April 2015 for use as an auxiliary engine in a container vessel, and this unit has been operating well without any serious problems. Periodical investigations are being conducted for component durability and the engine’s performance in an actual vessel to confirm reliability and durability over long-term use.
As the second step in the development, Yanmar also plans to embark on work that will bring improvements extremely in customer LCV by combining techniques that will further enhance performance and quality, such as variable valve mechanisms and two-stage turbocharging systems of which fundamental technologies have already been developed.
-IMPORTANT-
The original technical report is written in Japanese.
This document was translated by Research & Development Management Division.
Author
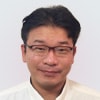