YANMAR KOTA KINABALU
R&D CENTER SDN. BHD.
YANMAR Technical Review
Research and Development of Marine Engine that Operates with Biofuel – Evaluation of Refined Breached Deodorized Palm Oil (RBDPO) –
Abstract
Since biofuels based on vegetable oil are considered to be carbon-neutral, CO2 emissions can be reduced by the amount of biofuel blended with fossil fuels. The test fuel is supplied to marine diesel auxiliary engine through a fuel blending system which mixes refined breached deodorized palm oil (RBDPO), which is not esterified, and heavy fuel oil (HFO). At first, conditions for stable fuel supply such as heating temperature were clarified. Then performance tests were performed to evaluate effect of blend ratio of RBDPO and HFO. It was decided that the 2000h-endurance test was possible by using 100% RBDPO from tests results. This endurance test had been completed for approximately 1500 hours at the time of writing this article, no significant problem has been observed so far.
1.Introduction
Considered to be carbon-neutral, biofuels based on vegetable oil reduce CO2 emissions when blended with fossil fuels in accordance with the amount of biofuel added. A number of countries are already using fatty acid methyl ester (FAME) made from straight vegetable oil (SVO) in diesel blends for automotive use. Lower CO2 emissions can be expected from the use of biofuels in marine diesel engines, and significant economic advantages can be expected as well if SVO is used as it is without processing it to FAME.
The research and development described in this article is selected for funding by a joint project of the Ministry of Land, Infrastructure, Transport and Tourism and Nippon Kaiji Kyokai for the development of next-generation marine environmental technology (timetable: 11/21/2013 – 3/31/2018), and is conducted at the Yanmar Kota Kinabalu R&D Center (YKRC) in Malaysia. An existing experimental apparatus was retrofitted with a blending system, and the biofuel is supplied as a blend with heavy fuel oil (HFO). The test fuels are two different palm oils: a refined bleached deodorized palm oil (RBDPO) and a crude palm oil (CPO) which are made from palm SVO. At the time of writing, however, the endurance testing of RBDPO is still in progress and therefore this report focuses on results prior to that point.
2.Fuel Blending System
The tests use a fuel blending system to mix palm oil with HFO. Fig. 1 shows a block diagram of the blending system. The blending system and a service tank to hold the blended fuel are retrofitted between the existing service tanks and fuel supply unit. Fig. 2 shows a detailed block diagram of the blending system. The blending system is equipped with flow meters to measure the flow of fuel from the service tanks holding palm oil and HFO respectively, and with valves to regulate the flow rates. It is designed so that the blending ratio can be controlled by adjusting the valves with reference to the flow meter readings. A signal from a float switch in the service tank for blended fuel is used to automatically operate the blending system to replenish the tank whenever the amount of fuel in the tank decreases below a specified level. To avoid unequal mixture of the flow-regulated palm oil and HFO l in a pipe an agitating unit (homogenizer) is also included to forcibly mix the two fuels.

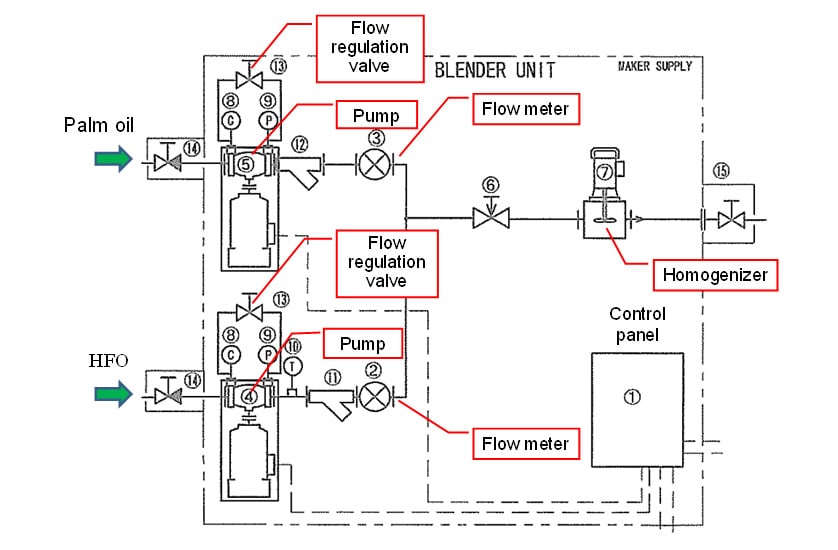
3.Characteristics and Subject for RBDPO
As shown in Fig. 3, the bulk of the world’s palm oil is produced in Indonesia and Malaysia, with total production in 2014 of approximately 61 million tons(1). Production in Malaysia was 19.8 million tons in 2014 and is planned to increase to 20.5 million tons in 2020 and 24.6 million tons in 2035, with 28% of Malaysia’s total domestic demand of 1.39 million tons in 2035 expected to be used for biofuel(2). These biofuel-producing nations are looking to adopt marine engines capable of operating using biofuel as a means of achieving local production and consumption.
RBDPO is a palm oil that a crude palm oil has been degummed, bleached, and deodorized. As shown in Fig. 4, it tends to separate into two layers when stored at room temperature (about 30℃), with a clear liquid layer forming on top of a milky gel-like layer. As RBDPO is a mixture of various different fatty acids, this gel-like material is thought of as components with a high melting point that have solidified out of that mixture. Fig. 5 shows the composition of fatty acids in RBDPO. (In the figure, the composition of fatty acids is categorized by the carbon number and number of double bonds. For example, a fatty acid with carbon number 18 and one double bond is indicated as "C18:1.") Generally, a smaller number of double bonds shows a higher melting point, with saturated fatty acids (with no double bonds) tending to have a higher melting point than unsaturated fatty acids (with double bonds). As approximately 40% of RBDPO consists of saturated fatty acids with a high melting point, it is assumed that the solid part at room temperature (about 30℃) is mainly made up of those compounds.
Fig. 6 shows a photograph of a filter equipped in the blending system fuel pipe through which RBDPO flows at room temperature (about 30℃) during testing. The filter is plugged with milky gel-like material, blocking the flow of fuel. As this plugging causes problems, some sort of countermeasure is needed when using a fuel that contains a high proportion of high-melting fractions of fatty acids like RBDPO.
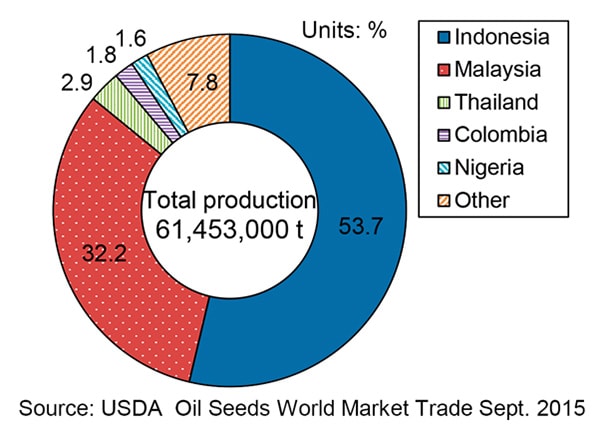



4.Countermeasures against Fuel Line Plugging
4.1.Study of Solidification and Melting Conditions for High-melting Fractions
High-melting fractions that plug filters and flow meters are required to prevent the solidification and to melt if solidified. Possible ways of achieving this include agitation and heating. Accordingly, the study varied the heating temperature and agitation conditions to investigate the conditions for solidification and melting of high-melting fractions.
4.1.1.Solidification Conditions for High-melting Fractions
The study first looked at conditions for the solidification of high-melting fractions. The effectiveness of agitation at different temperatures 20℃, 30℃, and 50℃ was investigated. RBDPO in the separated form shown in Fig. 4 (at 28℃) was left for 12 hours at each temperature and then compared. Fig. 7 shows the results, how agitation prevents the solid part from separating and allows it to be kept in a fluid state at a lower temperature than when agitation is not used. However, heating is needed to melt solidified high-melting fractions. From this it is evident that solidification and the buildup of high-melting fraction in the fuel tank and pipes are risks when using RBDPO, even in a tropical climate like that in Malaysia, because the solidification of high-melting fractions cannot be avoided. While heating is needed to prevent solidification, agitation disperses high-melting fractions throughout the tank, preventing them from collecting at the bottom and separating out.
4.1.2.Melting Conditions for High-Melting Fractions
The study next looked at the conditions for melting the high-melting fractions that is solidified. 100g of separated RBDPO was heated without agitation using a variety of initial and heating temperatures, and the time taken for the solid to fully melt was measured. Note that heating was performed by using water bath and the maximum time allowed for heating was 1800s. Fig. 8 is the result, which shows that the higher the initial or heating temperature, the shorter time it takes for the solid to melt. In the case of a heating temperature of 40℃, the solid is not fully melted even after 1800s. While a temperature of at least 50℃ is needed to melt solid high-melting fractions, the very long time taken to melt at temperatures below 60℃ indicates that heating to at least 60℃ is desirable in practice. As the RBDPO remains in entirely liquid form when tested with an initial temperature of 45℃, it is found that, if the all of high-melting fractions is liquid, the solidification can be prevented by maintaining a temperature of 45℃ or higher.


4.1.3.Oxidation and Degradation of Fuel Due to Heating
While the study has found that heating the fuel can prevent the solidification of high-melting fractions, there is a risk that this could result in degradation due to oxidation. To study the effect of fuel degradation due to heating, oxidation stability is evaluated using Rancimat. The test conforms to the EN14112 standard for the oxidation stability testing of biodiesel (FAME). While oxidation stability test is typically conducted at 110℃ with a bubbling air flow rate of 10L/h, the test in this case includes temperatures of 70℃ and 90℃ considering actual heating temperatures. Table 1 lists the test results. The oxidation stability at 70℃ and 90℃ exceeds 72 hours, which is an adequate length of time. The time was significantly short, approximately 26 hours at 110℃. While EN14214 specifies an oxidation stability standard for biodiesel of 6 hours or more, in order to prevent fuel degradation, it is desirable to set an upper limit of 90℃ for the heating temperature.
Table 1 RBDPO Oxidation Stability at Different Temperatures

4.2.Requirements for RBDPO Fuel Lines
In terms of the requirements for RBDPO fuel lines, the conclusions of the studies described in section 4.1. above can be summarized as follows.
(1)If heating of the entire fuel supply system is possible
Fuel solidification and the associated problems caused by plugging can be prevented by maintaining the tank, fuel pipes, and filters at a temperature of 45℃ or higher (up to 90℃).
(2)If heating of the entire fuel supply system is not practical
Heating the fuel line (60℃ to 90℃) immediately upstream is needed to prevent filters from plugging by solidified high-melting fractions. In the tank, it is possible to keep the fuel in liquid form at temperatures as low as about 20℃ by agitating it. For fuel lines, however, the potential for plugging when not in use means a heater is needed to maintain the temperature.
As the test apparatus used at YKRC is of the latter type (2), agitation is used to establish a circulating flow in the tank to prevent separation, and a heating circuit just upstream of the filter is used to prevent plugging due to the solidification of high-melting fractions. Trace heaters are also fitted to all pipes, both to prevent the solidification of high-melting fractions due to the decrease of fuel temperature, and to facilitate the re-start of test after a long time stop of the apparatus operation by melting any plugging.
5.Engine Test Using Different Blend Ratios
The effect of blend ratio of RBDPO and HFO on engine performance was tested by using the fuel blending system. The conditions of buildup of deposits on the fuel injectors, which are concerns with using vegetable oils, were also studied to determine the blend ratios for endurance tests. The target duration for the endurance tests is 2000 hours.
The test engine is a six-cylinder, vertical, water-cooled, four-stroke cycle diesel engine. Table 2 lists its specifications.
The fuels used in the test were blends of RBDPO and HFO. Table 3 lists the properties of the two fuels. RBDPO has a lower density, viscosity, and calorific value than HFO. Also, being a vegetable oil, RBDPO contains about 8% oxygen. The amount of oxygen in RBDPO is determined from the proportions of H, C, N, and S. The theoretical amount of air calculated from the fuel composition of RBDPO, which is oxygen-containing fuels, is approximately 3% lower than that of HFO because part of the oxygen required for combustion is supplied from the fuel itself.
Table 2 Engine Specifications

Table 3 Fuel Properties

5.1.Effect of Blend Ratio on Constant Speed Performance
To study the effect of blend ratio on performance, performance tests (30 minutes at each load) were conducted for a range of different RBDPO and HFO blends. The tests used D2 test cycle mode (ISO 8178-4), which is applied for an auxiliary marine engine. D2 mode includes performing measurements at 10%, 25%, 50%, 75%, and 100% load. General performance parameters, such as various temperatures (including charge air, exhaust, and cooling water) and pressures (including charge air and cooling water), as well as exhaust emissions, smoke, and fuel consumption were measured. The RBDPO blend ratio is varied from 0% (= 100% HFO) to 100% (= 100% RBDPO), and the fuel supply system controlled the kinetic viscosity within a range of 11-14 mm2/s (cSt) at the engine inlet.
Fig. 9 shows effects of the blend ratios on the engine combustion performance. Higher ratios of RBDPO results less smoke with the effect being particularly evident at low load. As RBDPO is an oxygen-containing fuel and the fuel spray itself can supply oxygen, the smoke is improved compared to HFO at a low load, where fuel injection pressure is low and spray atomization is not sufficient. As for exhaust emissions, although no significant difference in NOX is evident for different blend ratios, higher blend ratios result in lower THC and CO. This also is believed to be due to the promotion of combustion of an oxygen-containing fuel. Because these fuels have different calorific values, thermal efficiencies are compared instead of fuel consumption. A higher blend ratio improves efficiency, with maximum efficiency occurring for 100% RBDPO fuel. Thus, it can be concluded from these performance tests that 100% RBDPO provides low emissions and high thermal efficiency.

5.2.Effect of Blend Ratio on Low-load Performance (Smoke)
When using vegetable oil, it is generally found that deposits tend to build up around the fuel injector due to the insufficient vaporization of a spray due to vegetable oil having a higher distillation temperature compared to a fossil fuel. As deposits built up impedes the formation of the spray from the fuel injector and have other detrimental effects, in particular worsening in smoke, a potential problem for long-term operation is concerned. Performance tests for approximately 30 minutes at each load is inadequate for evaluating the effect of deposits, so short-duration endurance tests are conducted for each blend ratio to study the state of deposits built up and any worsening in smoke. As the high injection pressure at high load would tend to blow away any deposits built up, the tests were conducted at a low load of 25%. With reference to the operating pattern to be used in subsequent endurance test, a test duration of 8 hours at 25% load was chosen.
Fig. 10 shows the results of the 8-hour, low-load, smoke endurance tests. These results show that, whereas the smokes for blend ratio of 0% RBDPO (=100% HFO) and 100% RBDPO (=0% HFO) are relatively stable with no major variation in the level of smoke over time, although the levels themselves are different, a significant worsening in smoke occurs temporarily for low blend ratios (20 to 50% RBDPO). A phenomenon of worsening in smoke in the later stages of the test is seen for higher blend ratios (60 to 90% RBDPO), the absolute values are small compared to blends with a low percentage of RBDPO. Regarding the sudden worsening and then recovery of smoke for blend ratios of 20 to 50% RBDPO, it is believed to result from the forming of deposits and increasing of smoke as the deposits grew, and then the breaking off of those deposits, resulting in a sudden recovery. Fig. 11 shows a comparison of the worsening in smoke during the 8-hour, low-load, smoke endurance tests. The worsening in smoke (ΔSmoke) is defined as the difference between the maximum of smoke during the test and the smoke after four hours of operation, when the smoke is stabilized. The figure shows ΔSmoke increases as the proportion of RBDPO in the blend increases, reaching a peak at 30%, after which it decreases as the proportion of RBDPO increases even more, and ΔSmoke for a blend of 100% RBDPO is almost the same as that for a blend of 0% (= 100% HFO). Fig. 12 shows a comparison of deposits built up after the 8-hour smoke endurance tests. The amount of deposits tends to increase as the proportion of RBDPO in the blend increases, showing a different trend than that for the ΔSmoke which once increasing and decreasing after a certain point. The low ΔSmoke for high blend ratios of RBDPO is believed to be due to any detrimental effect on combustion being suppressed by the presence of the oxygen in RBDPO, even when deposits impede the supply of air to the spray. In contrast, when the blend percentage is low, although there is less deposits, the combustion is easily affected by insufficient air supply into the fuel spray due to the smaller proportion of oxygen-containing RBDPO and therefore the combustion of the HFO in the blended fuel is worsened.



5.3.Determination of Blend Ratio Based on 46-Hour Short Endurance Test
The results of the constant speed performance test and 8-hour, low-load, smoke test described above reveal that endurance test using 100% RBDPO fuel is possible however buildup of deposits is worse. To investigate how this buildup of deposits would affect performance in the actual endurance test mode, 46-hour (2 cycles × 23-hour) short endurance test is conducted prior to starting the 2000-hour endurance test to evaluate the deterioration in smoke at different loads. To investigate the effect of blend ratio, 46-hour short endurance test is performed using blend ratio of 30%, 50%, 80% and 100% RBDPO. Fig. 13 shows smoke during the 46-hour short endurance test. A deterioration in smoke is observed in cases other than 100% RBDPO. The deterioration is most evident in the second cycle and, in the case of 80% RBDPO, this deterioration was so bad that the test was aborted after 26 hours. In all cases, the deterioration in smoke in the second cycle began from the first mode in the cycle (25% load). This is believed that deposits accumulated during the first cycle promote to buildup of deposit significantly in the condition of 25% load, which is the condition deposits are easily built-up, at the start of second cycle.
The test results of the constant speed performance test, 8-hour, low-speed, smoke test and 46-hour short endurance test are summarized in Table 4, and RBDPO blend ratios used for 2000-hour endurance test are studied. The results of the 8-hour, low-speed, smoke test and 46-hour short endurance test, which evaluated the buildup of deposits indicates that performing endurance test for other than 100% RBDPO would be difficult with the deterioration in smoke, so it was decided that the initial 2000h-endurance test should be performed using 100% RBDPO.

Table 4 Review of RBDPO Blend Ratios in Endurance Tests

6.Progress of Endurance Test
The 2000h-endurance test using 100% RBDPO had been completed for approximately 1500 hours at the time of writing this article, with testing scheduled to continue up to 2000 hours. Fig. 14 shows smoke during endurance test. While the results of 8 hours, low-load, smoke endurance test and 46-hour short endurance test conducted prior to the endurance test had raised concerns that smoke may deteriorate after a time even when fueled by 100% RBDPO, no such significant deterioration has been observed so far. Fig. 15 shows the buildup of deposits on the fuel injector during 2000h endurance test. However, no significant increase in the amount of deposits is observed and it appears that repeated buildup and breaking off of deposits is occurring as the endurance test progresses.


7.Future Plans
This article has described the subjects and countermeasures identified for the use of RBDPO in marine engines, and the results of performance tests carried out in preparation for the endurance test. Once the endurance test is complete, the measurement of component wear is planned to evaluate the effects of the biofuel on the engines comprehensively. As noted earlier in the article, a further evaluation of CPO (palm oil in its raw form) is also planned after the test using RBDPO.
References
- (1)USDA, Oilseeds: World Markets and Trade, Sept. 2015
- (2)Gan & Li, IEEJ June 2012, A Study on Malaysia’s Palm Oil Position in the World Market to 2035
-IMPORTANT-
The original technical report is written in Japanese.
This document was translated by Research & Development Management Division.
Author
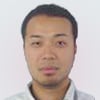