YANMAR Technical Review
The New TNV Engine Series : World’s First Engine Complies with Swiss PN Regulations
Abstract
The new TNV engine series was developed to satisfy customer demand while complying with strict emission regulations. Yanmar’s advanced combustion technology using a common rail injection system and cooled exhaust gas recirculation, which is controlled by a unique correction method, are used to achieve better engine performance. An exhaust after-treatment system is adopted for cleaner emissions. A total engine management system using Yanmar’s original software maintains optimal engine performance by itself, by adjusting the engine operating parameters automatically based on physical models. It also helps to achieve reliable DPF regeneration using a unique regeneration strategy without changing the feel of engine operation. It also has the advantage of enabling very flexible designs.
1. Background
Because diesel engines have low fuel consumption and excellent durability and reliability, they are widely used as a power source for industrial machinery. On the other hand, as concern for the global environment increases worldwide, emission regulations have become gradually stricter even for industrial diesel engines. Table 1 shows emission regulations in different countries. Tier 4 regulations (USA) and Stage 3B regulations (EU) have been enforced since 2013, and Tier 3 regulations for non-road special motor vehicles (Japan) have been enforced since 2014. These regulations reduce the emission of particulate matter (PM) to one tenth of the previous regulation values. Also, in Switzerland, regulations have been introduced for particulate number (PN), the number of PM. This is part of a trend of strengthening regulation of PM in particular. Fig. 1 shows the test cycle that has been added from the Tier 4 regulations in the USA. Tier4 engines must meet not only the previous steady state test cycle but also transient test cycle (NRTC). In addition, engines must also meet not-to-exceed (NTE) standards that limit emission under various work and environmental conditions. In this way, regulations are becoming more complex. To comply with such regulations, more advanced technology and completely new technology must be developed.
Yanmar has been working collectively as a company and utilizing its diesel combustion technologies cultivated over the years. The result was the market launch in 2013 of the new TNV engine series, which complies with the strict emission regulations described above and is the optimum power source for industrial machinery, enabling easy use regardless of the operating environment or operation methods. This article describes the technologies for compliance with emission regulations and the product strengths of the new TNV engine series.


2. Product Overview
Fig. 2 shows an overall view of a new TNV engine. The new TNV engine series is comprised of products developed to be even cleaner than before, without impairing the fuel consumption, high power, reliability, and low noise performance that were characteristic of the previous models. Innovations have been introduced not only to hardware, but also to software, achieving high performance suitable for the engine operating conditions and environment. The selection of optimum devices and maintaining the same engine sizes as previous models provides flexibility for installation in a wide range of operating machines, and replacing previous model engines with the new one is also easy.

3. Engine Lineup
Fig. 3 shows the lineup of the new TNV engines. They are offered with outputs from 6 kW to 56 kW to meet a wide range of customer needs.

4. Applied Technology
Fig. 4 shows an overview of devices used in the new TNV engines. New devices such as a common rail system and cooled exhaust gas recirculation (EGR) are used to comply with the strict Tier 4 regulations. Also, a diesel particulate filter (DPF) is used as an exhaust after-treatment system to maintain clean emission and good operability in high load ranges, at which PM emissions from the engine increase. However, when the DPF accumulates PM from the exhaust gas, the exhaust pressure rises and excessive EGR is performed, causing the PM amount to increase. For this reason, the EGR ratio must be controlled to an appropriate level to reduce the risk of DPF clogging and the frequency of DPF regeneration. Also, because the allowable time to stop operations for DPF regeneration are limited in industrial machinery, there is a need to perform reliable regeneration while the engine is in use. Further, as an industrial engine, the same flexibility as previous models is required to enable installation in a wide range of operating machines with different layouts.
To meet these requirements, Yanmar adopted new devices and an innovative control software. Yanmar's original total engine management system calculates the conditions of engine and components based on a physical model to perform the optimum engine control according to the operating conditions. Installing this control system in the engine control unit (ECU) has reduced the risk of DPF clogging and the regeneration frequency as well as emissions. Also, Yanmar has developed its original regeneration control system to achieve reliable DPF regeneration in a wide variety of operating machines and work patterns. Further, the adoption of a control system that does not use an air flow sensor eliminates the man-hours required for making adjustments for each layout, making it easy to install the engine in operating machines.
By using new technologies in both hardware and software, as described above, Yanmar achieved the subjects to make the engines complying with Tier 4 regulations, resulting in strong product appeal.

5. Environmental Performance
5.1. Exhaust Emissions
Fig. 5 shows evaluation results of PM and NOX+NMHC emissions. 4TNV88-B engine, which is certified by EPA for Tier 3 regulations, emissions exceed the Tier4 regulation limit in NOX + NMHC and PM emissions. NOX+NMHC emission is reduced with using common rail injection system and cooled EGR without increase in PM emission with 4TNV88C. PM is reduced to one tenth of the previous level with employing DPF system. As a result, the new TNV engine series have achieved the strict Tier 4 regulation values.

5.2. PN (Particulate Number)
Fig. 6 shows the measured results for PN. The new TNV engines use a DPF to greatly reduce the PN and achieve the regulation values. As a result, in the 19 to 37 kW output range, this engine is the first in the world to acquire certification for complying with the PN regulations enacted by Switzerland. It should be noted that PN regulations are under discussion in Europe to be introduced in the Stage V regulations that are currently set to go into effect from 2019. As of 2013, Yanmar's new TNV engine series had the potential to comply with these regulations.

6. Product Strengths
6.1. DPF Clogging Risk Reduced by Yanmar's EGR Control
In engines equipped with a DPF, when the exhaust pressure rises due to PM accumulation as previously described, or when atmospheric conditions change, the EGR gas amount must be controlled to an appropriate level to maintain DPF quality. Fig. 7 shows the results of an evaluation of the EGR ratio, NOX, and smoke in the case of high exhaust pressure and low atmospheric pressure (high altitude conditions). As the exhaust pressure and atmospheric pressure change, the EGR gas flow is controlled to an appropriate level by Yanmar's original engine control, and by restricting the increase of smoke, the DPF clogging risk and regeneration frequency are reduced.

6.2. Work Efficiency Improved by Yanmar's DPF Regeneration Control
Periodic regeneration of the DPF is needed to remove the PM accumulated in the filter. Fig. 8 shows an overview of Yanmar's DPF regeneration control. Yanmar has independently developed a "three-step regeneration control" system. This is comprised of (1) "Assist regeneration" that does not use post injection (2) "Reset regeneration" that uses post injection, and (3) "Stationary regeneration" that stops work to perform complete regeneration. This control enables regeneration even in low-speed low-load operations where DPF regeneration has usually been difficult, as shown in Fig. 9. This achieves perfect regeneration regardless of the operating machine or work pattern. In addition, the adoption in this control of assist regeneration that does not use post injection achieves regeneration with low fuel consumption.
These controls result in a highly reliable system that achieves both reliable regeneration and low fuel consumption, which increases the work efficiency of customers.
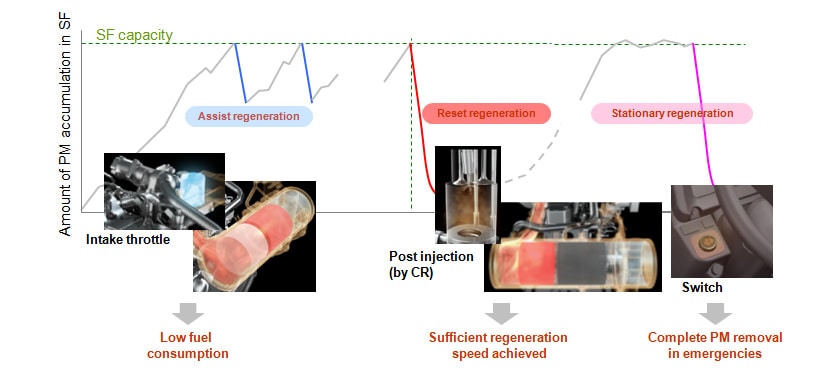

6.3. Flexibility for Installation in Various Operating Machines
In the control described above, it is important to control the EGR to an appropriate level, and measure the air intake flow in order to perform reliable regeneration. Air intake flow measurement is usually performed in automobile engines with an air flow sensor. However, the air flow sensor tends to be affected by the air intake layout, requiring adjustments to be made for each layout. In an industrial engine that requires installation in a wide variety of operating machines, these adjustments require many man-hours, resulting in a major obstacle to installation.
Fig. 10 shows examples of operating machines in which the new TNV engines can be installed. Yanmar has created a control system that does not use an air flow sensor. This eliminates the adjustment man-hours required for installation, providing flexibility that can be easily installed in various types of operating machines.

7. Conclusions
Yanmar has developed the new TNV engine series to comply with strict emission regulations while also satisfying customer demand for performance such as power, fuel consumption, and work efficiency. These are summarized below.
- Advanced combustion technology, and a common rail system and a cooled EGR system controlled by an original method are combined to achieve high performance for various operating machines and work conditions.
- DPF, an exhaust after-treatment system, has been adopted to achieve strict PM regulations, and this engine is the first in the world to acquire certification for complying with the PN regulations enacted by Switzerland.
- Yanmar's original DPF regeneration control results in a highly reliable system that achieves both reliable regeneration and low fuel consumption, which increases the work efficiency of customers.
- The adoption of a control system that does not use an air flow sensor eliminates the man-hours required for making adjustments for each layout, making it easy to install the engine into operating machines.
Yanmar released the new TNV engine series to the market in 2013, and since then it has been highly rated by customers. Industrial engines face an ever-changing environment, with emission regulations becoming stricter and operating machines becoming more advanced. In the future, Yanmar will continue to seek value from the perspective of our customers and make our best efforts to provide them with optimal solutions.
Finally, the authors would like to extend our heartfelt thanks to everyone who supported and cooperated in the development of the new TNV engine series.
-IMPORTANT-
The original technical report is written in Japanese.
This document was translated by R&D Management Division.
Author
Engine Development Division
Power System Operations Business