News Release
Looking back at the exceptional engine testing of a special vessel Berlin-Ramelau of Damen shipyard
April 29, 2022
Yanmar Europe B.V.
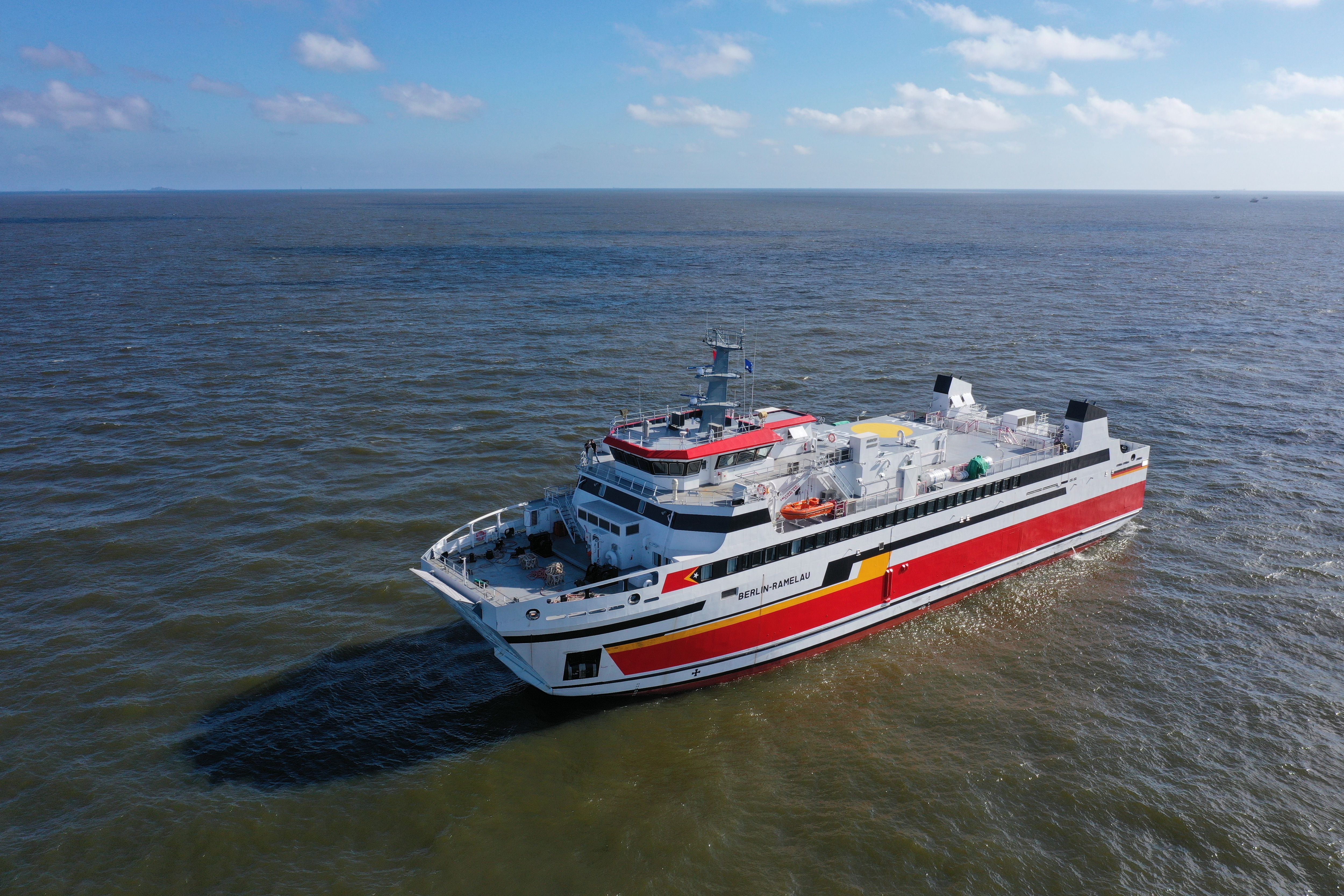
The Berlin-Ramelau entered service on a route between the Timor-Leste capital Dili, the Oecusse enclave and the island of Ataúro in Southeast Asia. The sea trials were successful and now the owners at the Timor-Leste government have completed crew training. The vessel is 67-metres long and passenger capacity is up to 308, with space for vehicles and cargo.
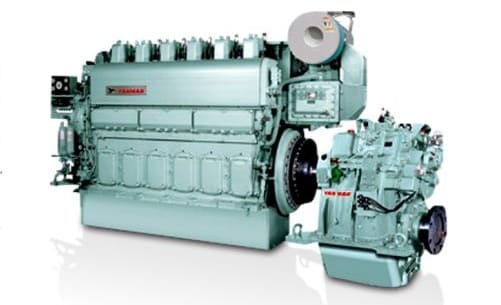
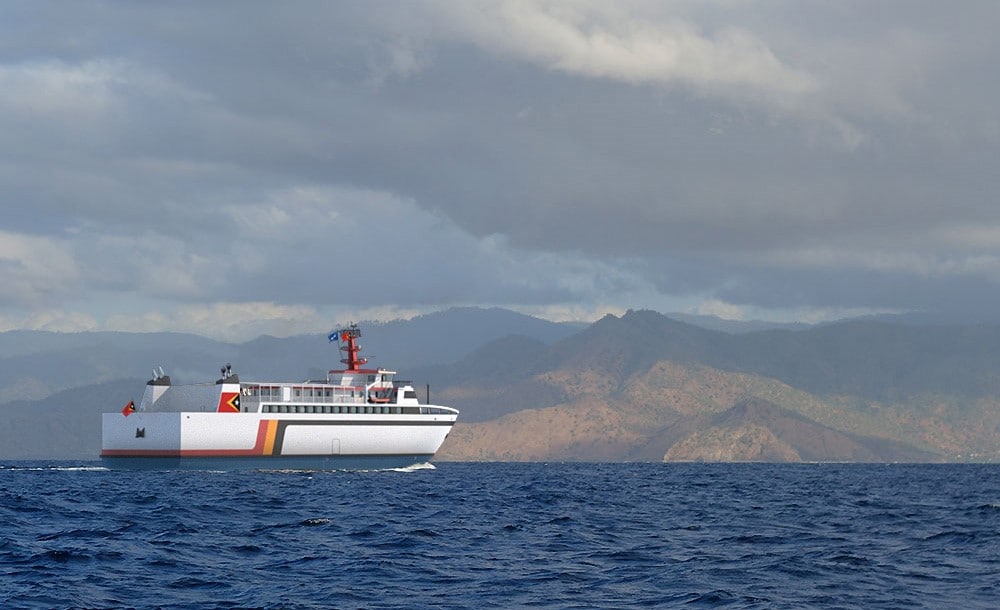
Built by Damen Shipyards Group at its Yichang Shipyard in China, she’s equipped with two 6-cylinder medium duty Yanmar Y17W engines. Elly Kortleve from the comms team at the shipyard says, “Like any new purpose-built vessel, this one is unique! The most important requirements for a RoPAX ferry like this, concern reliability and maintenance. These vessels provide a lifeline between communities. The choice for a reliable engine with a good local service network is therefore of the upmost importance and helps Timor-Leste in providing the most reliable service possible.”
The engines, which run at 1,350RPM, are attached to a gearbox supplied by Reintjes which has a reduction ratio of 5.05. The output speed is around 287RPM, enabling the most efficient torque delivery.
Kortleve continues, “When choosing an engine there are a number of different requirements which are set at the design stage. These requirements differ per ship type and operational area but always include a comparison based on fuel consumption, weight, RPM and power at service speed, local supply of spares and maintenance requirements. The Yanmar engines have been selected because of the broad and highly professional service network in the Southeast Asian region plus the stability of supply with genuine Yanmar parts, which significantly reduces maintenance time and increases operating time for the operator.”
Yanmar also provided the ship with two 6HAL2-WHT gensets, providing 265kW at 1,800RPM.
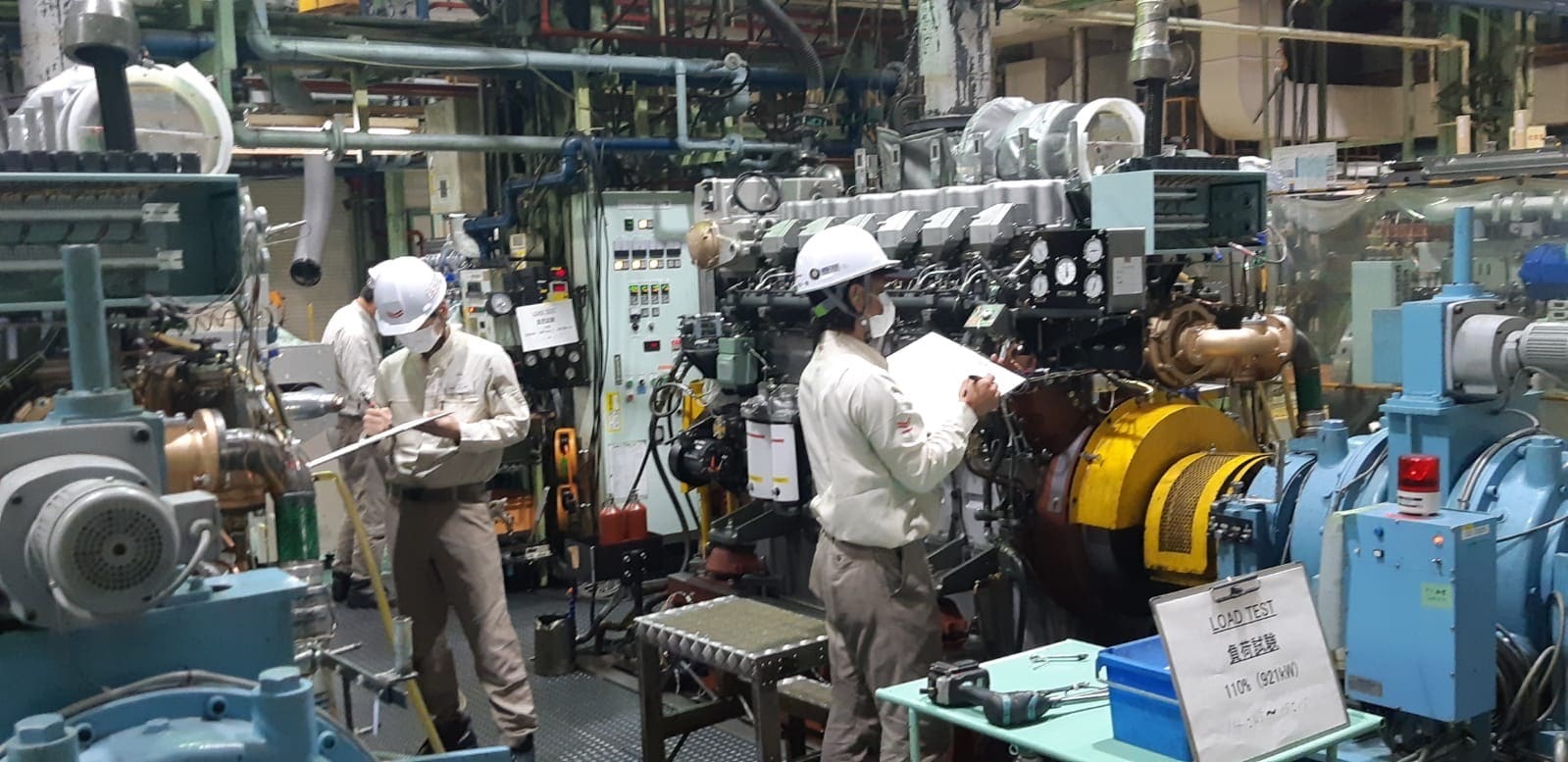
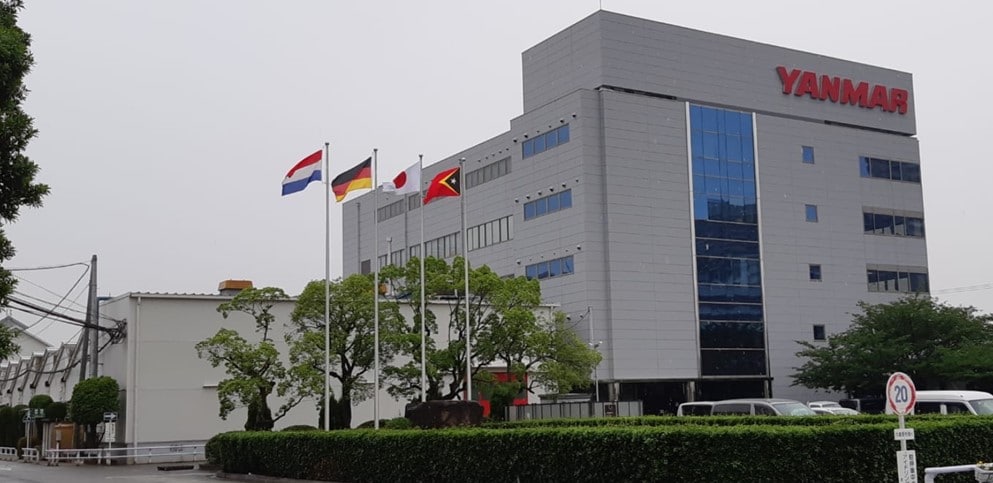
Prior to delivery, the engines underwent the usual factory acceptance tests, but with the restrictions bought about by the pandemic, a novel format was devised to allow virtual attendance of all the interested parties. It’s a standardised procedure lasting around four and a half hours. It’s normal for all marine units to be shipped, even for small pleasure boat engines which are produced in Almere.
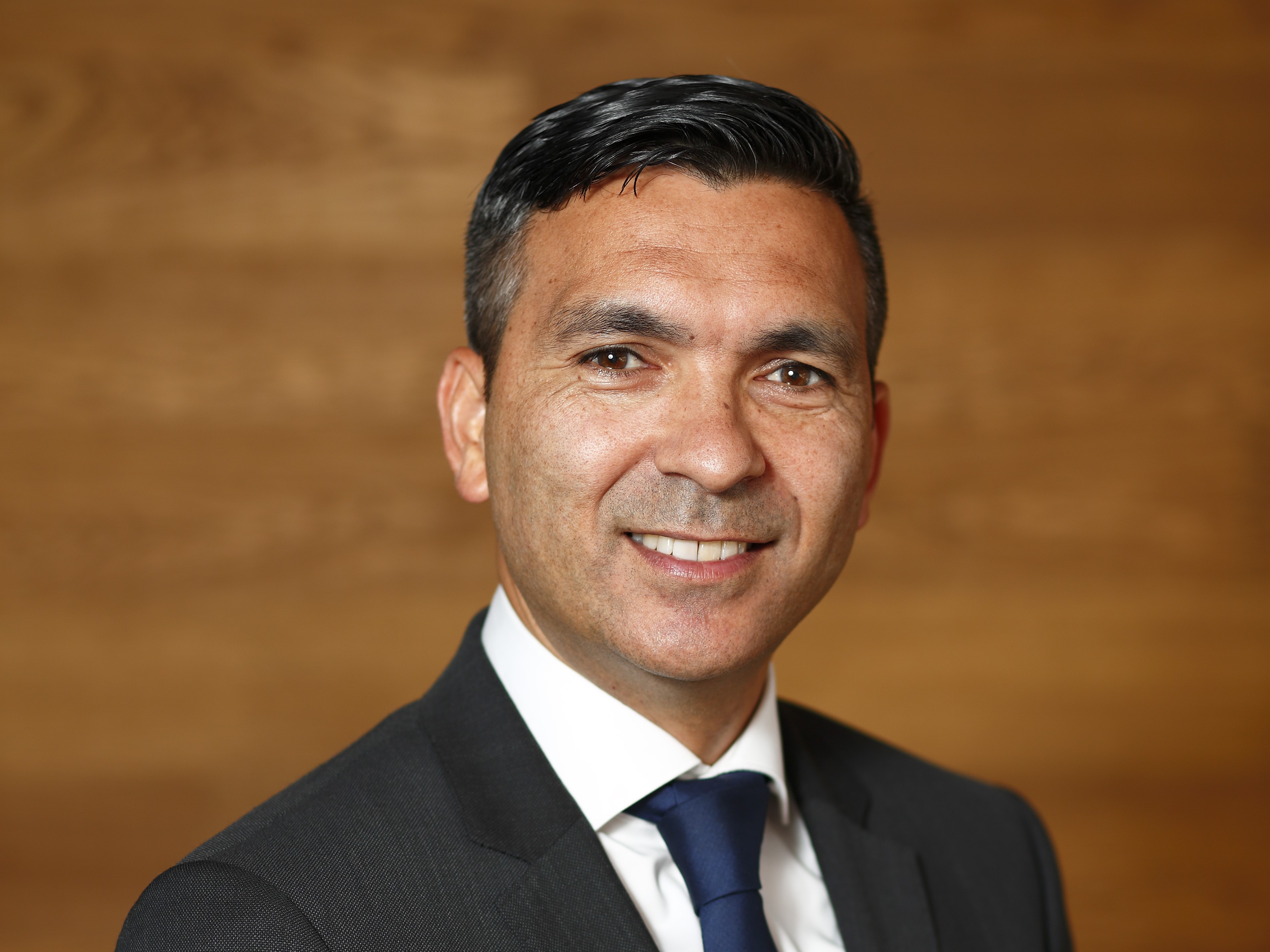
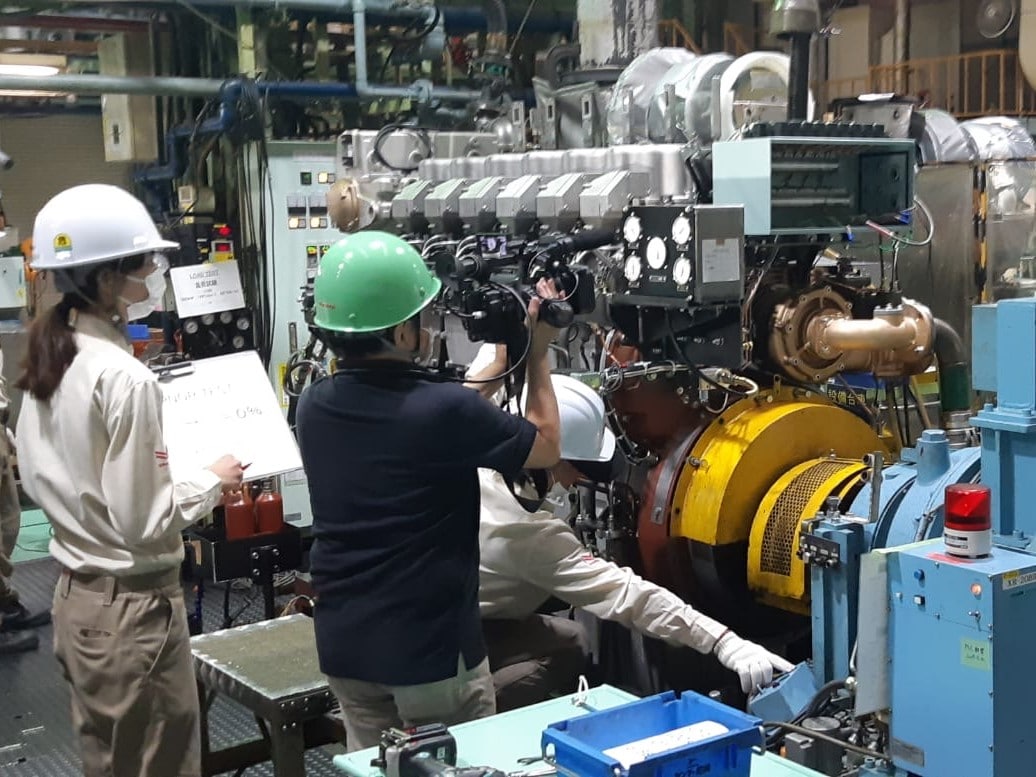
Richard Lesteluhu is the area manager at Yanmar Europe’s commercial marine department. He explains, “The factory acceptance test guarantees that the equipment complies with all the requirements as requested and is ‘ready to be commissioned’ without any problems. It is beneficial for both the end-users and the manufacturer. Any functional issues are identified before the equipment leaves the factory so can be rectified immediately, so the FAT helps in controlling the project timeline and cost. If a problem is found after the equipment is installed, it may result in costly shutdowns. Also it provides a number of other benefits such as checking accessibility requirements for operation and maintenance, checking the location of tie-in connection points, ensuring compliance with the original specifications and it’s a useful insurance to prove we produced what was promised.”
Normally this is easy. Yanmar arranges the test and informs the customer/operator ten days before hand, and they attend to scrutinise the outcome. However, pandemic travel and social mixing restrictions meant that this was impossible. Undaunted, engineers adapted and reorganised.
Lesteluhu continues, “We did it all remotely. My Japanese colleague Mizuhara-san set up a live stream via Skype. We had an array of fixed cameras and a mobile one to go wherever it was required. Altogether there were 23 observers in virtual attendance including the Timor-Leste government representatives, German consultants, financial stakeholders, representatives from the Damen Yichang Shipyard in China and our own manufacturing parties. They all followed on the live stream.”
Although the Yanmar team had never done anything like this before, it proved a success. Every aspect of the testing procedure was recorded and the customer was delighted. It’s proven to be an interesting exercise. At the forefront in everyone’s minds was safety, as having a camera operator roaming around a test bench is not a normal procedure. Also, in future other IT instruments could be bought in to optimise the process, for example for checking the sound during start-up. “It’s been a useful learning curve,” notes Lesteluhu. “There are pros and cons. Setting up the cameras has a cost, and by doing things remotely it deprives the customer of the opportunity to tour the factory which is a shame. However, we have proved that this remote method works and if customers request it in the future it can be done.”
Press Release Download
Inquiries
Yanmar Europe B.V., Marketing Dept.
Dana van Kammen
dana_vankammen@yanmar.com
- Note: Information contained in the news release is valid at the time of publication and may differ from the most recently available information.